
车削时,加工细长光轴的装夹方法
1个回答
关注
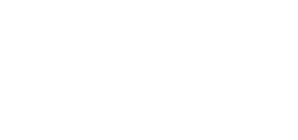
展开全部
(一)由于细长轴本身刚性差(L/d值愈大,刚性愈差),在车削过程中会出现以下问题:
1. 工件受切削力,自重和旋转时离心力的作用,会产生弯曲,振动,严重影响其圆柱和表面粗糙度。
2. 在切削过程中,工件受热伸长产生弯曲变形;车削就很难进行,严重时会使工件在顶尖间卡住。因此,车削细长轴是一种难度较大的加工工艺。虽然在车削细长轴的难度较大,但也有一定的规律性,主要抓住中心架、跟刀架的使用,解决工件热变形伸长以及合理选择车刀几何形状等三各关键技术,问题就迎刃而解了。
(二)使用中心架支承车细长轴
在车削细长轴时,可使用中心架来增加工件刚性。一般在车削细长轴使用的方法有:
1. 中心架直接来支承工件中间 当工件可以分段车削时,中心架支承在工件中间,这样支承,L/d减少了一半,细长轴车削时的刚性可增加好几倍。在工件装上中心架之前,必须在毛坯中部车出一段支承爪的沟槽,表面粗糙度及圆柱度误差要小,否则会影响工件的精度。车削时,中心架支承在工件中间与工件接触处应经常加润滑油。为了使支承爪与工件保持良好的接触,也可以在中心架支承爪与工件之间加一层砂布或研磨剂,进行研磨抱合。
2. 用过渡套筒支承车细长轴 用上述方法车削支承中心架的沟槽是比较困难的。为了解决这个问题,可加用过渡套筒的表面接触。过渡套筒的两端各装有四个螺钉,用这些螺钉套筒外圆的轴线与主轴旋转线重合,即可车削。
3. 使用跟刀架支承车削细长轴 跟刀架固定在床鞍上,一般有两个支承爪,跟刀架可以跟随车刀移动,抵消径向切削时可以增加工件的刚度,减少变形。从而提高细长的型状精度和减小表面粗糙度。从跟刀架的设计原理来看,只需两只支承爪就可以了,因车刀给工件的切削抗力Fr,使工件贴住在跟刀架的两各支承爪上。但实际使用时,工件本身有一个向下重力,以及工件不可避免的弯曲,因此,当车削时,工件往往因离心力瞬时离开支承爪,接触支承爪而产生振动。如果采用三只支承爪的跟刀架支承工件一面由车刀抵住,使工件上下,左右都不能移动,车削时稳定,不易产生振动。因此车削细长轴时一个非常关键的问题是要应用三爪跟刀架。
咨询记录 · 回答于2023-12-30
车削时,加工细长光轴的装夹方法
您好,我正在帮您查询相关的信息,马上回复您。
# 1. 选择合适的装夹方法
在车床上车削细长轴采用的两种传统装夹方式中,采用双顶尖装夹,工件定位准确,容易保证同轴度。但用该方法装夹细长轴,其刚性较差,细长轴弯曲变形较大,而且容易产生振动。因此只适宜于安装长径比不大、加工余量较...
# 2. 采用合理的车削方法
采用反向切削法车削细长轴。这样在加工过程中产生的轴向切削力使细长轴受拉,消除了轴向切削力引起的弯曲变形。
(一)由于细长轴本身刚性差(L/d值愈大,刚性愈差),在车削过程中会出现以下问题:
1. 工件受切削力,自重和旋转时离心力的作用,会产生弯曲,振动,严重影响其圆柱和表面粗糙度。
2. 在切削过程中,工件受热伸长产生弯曲变形;车削就很难进行,严重时会使工件在顶尖间卡住。因此,在车削细长轴是一种难度较大的加工工艺。虽然在车削细长轴的难度较大,但也有一定的规律性,主要抓住中心架、跟刀架的使用,解决工件热变形伸长以及合理选择车刀几何形状等三各关键技术,问题就迎刃而解了。
(二)使用中心架支承车细长轴。
在车削细长轴时,可使用中心架来增加工件刚性。一般在车削细长轴使用的方法有:
1. 中心架直接来支承工件中间 当工件可以分段车削时,中心架支承在工件中间,这样支承,L/d减少了一半,细长轴车削时的刚性可增加好几倍。在工件装上中心架之前,必须在毛坯中部车出一段支承爪的沟槽,表面粗糙度及圆柱度误差要小,否则会影响工件的精度。车削时,中心架支承在工件中间与工件接触处应经常加润滑油。为了使支承爪与工件保持良好的接触,也可以在中心架支承爪与工件之间加一层砂布或研磨剂,进行研磨抱合。
2. 用过渡套筒支承车细长轴 用上述方法车削支承中心架的沟槽是比较困难的。为了解决这个问题,可加用过渡套筒的表面接触。过渡套筒的两端各装有四个螺钉,用这些螺钉套筒外圆的轴线与主轴旋转线重合,即可车削。
3. 使用跟刀架支承车削细长轴 跟刀架固定在床鞍上,一般有两个支承爪,跟刀架可以跟随车刀移动,抵消径向切削时可以增加工件的刚度,减少变形。从而提高细长的型状精度和减小表面粗糙度。从跟刀架的设计原理来看,只需两只支承爪就可以了,因车刀给工件的切削抗力Fr,使工件贴住在跟刀架的两各支承爪上。但实际使用时,工件本身有一个向下重力,以及工件不可避免的弯曲,因此,当车削时,工件往往因离心力瞬时离开支承爪,接触支承爪而产生振动。如果采用三只支承爪的跟刀架支承工件一面由车刀抵住,使工件上下,左右都不能移动,车削时稳定,不易产生振动。因此车削细长轴时一个非常关键的问题是要应用三爪跟刀架。