
注塑产品表面有熔接痕怎么解决?
1个回答
关注
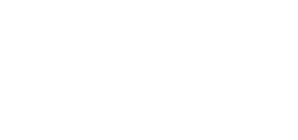
展开全部
注塑产品表面有熔接痕怎么解决:>熔接痕调整方法:1、减少浇口数量。2、调整浇口位置。3、在熔合部附近增设材料溢料井,将熔合线移至溢料井,然后再将其切除。4、在熔合线区域加强排气,快速疏散此部分的空气及挥发物。升高料温与模温,增强塑料的流动性,提高融合时的料温。5、改变浇口位置、数目,将发生熔合线的位置移往他处。6、增大注射速度。7、提高注射压力,适当增加浇注系统尺寸。8、减少脱模剂的使用。9、缩短浇口与熔接区域的距离。10、调整浇口位置,使塑料熔体通过浇口后碰撞销类或壁面。11、改变浇口形式,采用重叠浇口或凸耳浇口,在浇口区域设置足够的滞料区域。12、可减慢塑料熔体的初段注射速度。13、增大浇口厚度/横截面积,使流动前锋立即形成。14、升高模具温度,防止材料快速固化
咨询记录 · 回答于2022-10-20
注塑产品表面有熔接痕怎么解决?
注塑产品表面有熔接痕怎么解决:>熔接痕调整方法:1、减少浇口数量。2、调整浇口位置。3、在熔合部附近增设材料溢料井,将熔合线移至溢料井,然后再将其切除。4、在熔合线区域加强排气,快速疏散此部分的空气及挥发物。升高料温与模温,增强塑料的流动性,提高融合时的料温。5、改变浇口位置、数目,将发生熔合线的位置移往他处。6、增大注射速度。7、提高注射压力,适当增加浇注系统尺寸。8、减少脱模剂的使用。9、缩短浇口与熔接区域的距离。10、调整浇口位置,使塑料熔体通过浇口后碰撞销类或壁面。11、改变浇口形式,采用重叠浇口或凸耳浇口,在浇口区域设置足够的滞料区域。12、可减慢塑料熔体的初段注射速度。13、增大浇口厚度/横截面积,使流动前锋立即形成。14、升高模具温度,防止材料快速固化
气孔解决方式: l)调整成型条件,提高流动性。如,提高树脂温度、提高模具温度、提高注射压力及速度等。 2)增设排气槽,在熔接痕的产生处设置推出杆也有利于排气。 3)尽量减少脱模剂的使用。 4)设置工艺溢料并作为熔接痕的产生处,成型后再予以切断去除。 5)若仅影响外观,则可改变烧四位置,以改变熔接痕的位置。或者将熔接痕产生的部位处理为暗光泽面等,予以修饰。 异常现象产品原因解决方法: 裂纹 1.模具太冷 调整模具温度 2.冷却时间太长 降低冷却时间 3.塑料和金属嵌件收缩不一样 对金属嵌件预热 4.顶出装置倾斜不平衡,顶出截面积小或分布不当 调整顶出装置或合理安排顶杆数量及其位置 5.制作斜度不够,脱模难 正确设计脱模斜度 制品表面有波纹 1.物料温度低,拈度大 提高料温 2.注射压力 料温高,可减少注射压力,反之则加大注射压力 3.模具温度低 提高模具温度或增大注射压力 4.注射速度太慢 提高注射速度 5.浇口太小 适当扩展浇口 制品脆性强度下降 1.料温太高,塑料分解 降低料温,控制物料在料筒内滞留时间 2.塑料和嵌件处内应力过大 对嵌件预热,保证嵌件周围有一定厚度的塑料 3.塑料回用次数多 控制回料配比 4.塑料含水 原料预热干燥 脱模难 1.模具顶出装置结构不良 改进顶出设计 2.模腔脱模斜度不够 正确设计模具 3.模腔温度不合适 适当控制模温 4.模腔有接缝或存料 清理模具 5.成型周期太短或太长 适当控制注塑周期 6.模芯无进气孔 修改模具 制品尺寸不稳定 1.机器电路或油路系统不稳 修正电器或油压系统 2.成型周期不一样 控制成型周期,使一致 3.温度。时间。压力变化 调节,控制基本一致 4.塑料颗粒大小不一 使用均一塑料 5.回收下脚料与新料混合比例不均 控制混合比例,使均匀 6.加料不均 控制或调节加料均匀 制件脱皮分层 1.不同塑料混杂 采用单一品种的塑料 2.同一塑料不同牌号混杂 采用同牌号的塑料 3.塑化不良 提高成型温度 4.混入异物 清理原材料,出去杂质 熔接痕 1.塑料温度太低 提高机筒。喷嘴及模具温度 2.浇口太多 减少浇口或改变浇口位置 3.脱模剂过量 采用雾化脱模剂。减少用量 4.注射速度太慢 提高注射速度 5.模
5.成型周期太短或太长 适当控制注塑周期 6.模芯无进气孔 修改模具 制品尺寸不稳定 1.机器电路或油路系统不稳 修正电器或油压系统 2.成型周期不一样 控制成型周期,使一致 3.温度。时间。压力变化 调节,控制基本一致 4.塑料颗粒大小不一 使用均一塑料 5.回收下脚料与新料混合比例不均 控制混合比例,使均匀 6.加料不均 控制或调节加料均匀 制件脱皮分层 1.不同塑料混杂 采用单一品种的塑料 2.同一塑料不同牌号混杂 采用同牌号的塑料 3.塑化不良 提高成型温度 4.混入异物 清理原材料,出去杂质 熔接痕 1.塑料温度太低 提高机筒。喷嘴及模具温度 2.浇口太多 减少浇口或改变浇口位置 3.脱模剂过量 采用雾化脱模剂。减少用量 4.注射速度太慢 提高注射速度 5.模具温度太低 提高模温 6.注射压力太小 提高注射压力 7.模具排气不良 增加模具排气孔 注射不满 1.机筒及喷嘴温度偏低 提高机筒及喷嘴温度 2.模具温度偏低 提高模具温度 3.加料量不够 适当增加下料量 4.制件超过注射成型机最大注射量 选用注射量更大的注射机 5.流道及浇口太小 适当增加浇口尺寸 6.注射压力太低或注射速度太慢 提高注射压力或提高温度,提高注射速度
已赞过
评论
收起
你对这个回答的评价是?