
加工中心四轴速度怎么调整
1个回答
关注
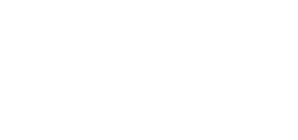
展开全部
要调整加工中心的四轴速度,通常需要进行以下步骤:
1. 进入程序编辑模式:首先,您需要进入加工中心的程序编辑模式。这可以通过机器控制面板上的相关按钮或菜单选项来完成。
2. 查找相关参数:在程序编辑模式下,您可以查找和调整与四轴速度相关的参数。这些参数通常以字母开头,如S、F、R等。具体的参数名称和表示意义可能因加工中心的型号和控制系统而有所不同。
3. 调整四轴速度参数:找到与四轴速度相关的参数后,您可以根据需要进行调整。根据实际要求,您可以逐步增加或减少速度值。确保根据加工要求和材料特性进行适当的调整。
4. 保存和验证更改:在完成速度参数的调整后,确保保存更改并进行验证。您可以运行一些简单的程序或进行手动操作来确保四轴速度调整后能够按照预期工作。
咨询记录 · 回答于2023-12-27
加工中心四轴速度怎么调整
问一个问题,但在某些特殊产品为什么要降低主轴转速,目的是什么?
调整加工中心的四轴速度通常需要进行以下步骤:
1. 进入程序编辑模式
要进入加工中心的程序编辑模式,您需要使用机器控制面板上的相关按钮或菜单选项。在程序编辑模式下,您可以进行四轴速度的调整。
2. 查找相关参数
在程序编辑模式下,您可以查找与四轴速度相关的参数。这些参数通常以字母开头,如S、F、R等。具体的参数名称和表示意义可能因加工中心的型号和控制系统而有所不同。
3. 调整四轴速度参数
找到与四轴速度相关的参数后,您可以根据需要进行调整。根据实际要求,您可以逐步增加或减少速度值。确保根据加工要求和材料特性进行适当的调整。
4. 保存和验证更改
在完成速度参数的调整后,确保保存更改并进行验证。您可以运行一些简单的程序或进行手动操作来确保四轴速度调整后能够按照预期工作。
在某些特殊产品加工过程中,降低主轴转速可能有以下几个目的:
1. 提高加工精度:降低主轴转速可以减少切削速度,这有助于提高加工的精度和表面质量。对于需要高度精密的零件或需要进行细小切削的工作,减慢主轴转速可以减少刀具的磨损和热变形,从而提高加工质量。
2. 避免振动和共振:在某些情况下,高速旋转的主轴可能会引起振动和共振问题。通过降低主轴转速,可以减少振动和共振的可能性,提高加工的稳定性和可靠性。
3. 处理特殊材料:某些特殊材料,如高温合金、硬质合金等,由于其硬度和韧性特性,加工时需要采用较低的主轴转速。降低主轴转速可以减少切削过程中对刀具的磨损,提高切削效率和工具寿命。
4. 执行复杂加工操作:在某些复杂的加工操作中,降低主轴转速可以提供更多的切削时间和稳定性,使加工过程更容易控制。例如,当需要进行细微刻度的铣削、螺纹加工或深孔钻削时,降低主轴转速可以提供更高的加工控制能力。
大宇精雕机的主轴最高转速和最低转速分别是多少?转速数值越高切削力就越快、转速数值越小切削力就越小、但在某些特殊产品为什么要降低主轴转速?目的是什么?知道答案吗
关于为什么在某些特殊产品中需要降低主轴转速的问题,原因有以下几点:
1. 刀具材料和切削要求:
* 某些材料,如硬质合金、高温合金等,由于其硬度和韧性特性,需要较低的主轴转速来避免切削过程中刀具过热和过快磨损。
* 降低主轴转速可以减少切削力,提高切削效率和工具寿命。
2. 加工精度和表面质量:
* 一些特殊产品可能对加工的精度和表面质量要求较高。
* 降低主轴转速可以降低切削速度,减少振动和共振引起的加工误差,从而提高加工精度和表面质量。
3. 可控性和稳定性:
* 在某些复杂的加工操作中,降低主轴转速可以提供更多的切削时间和稳定性。
* 例如,当需要进行细微刻度的铣削、螺纹加工或深孔钻削时,降低主轴转速可以提供更高的加工控制能力。
4. 安全性考虑:
* 降低主轴转速也可以增加加工过程的安全性。
* 特定产品加工可能涉及特殊的材料性质、刀具和加工条件,降低主轴转速可以减少事故的风险,确保操作人员和设备的安全。
精雕机平面铣削的计算方法,(列如:来料产品规格为:151.5*101.5*4、实际要求尺寸为150*100*4)、进力1间距0.1mm、一共要给多少刀?写出计算方法?答案是什么?
对于精雕机平面铣削的计算方法,以下是一种常用的计算步骤:
1. 确定切削刀具:选择适合平面铣削的刀具类型,例如平面铣刀。
2. 计算铣削次数:根据实际要求尺寸和加工公差,计算需要进行多少次铣削。这里以规定的进力1间距0.1mm为例,计算方法如下:
* X 方向上需要铣削的次数:(来料规格 - 实际要求)/ 进力1间距
* Y 方向上需要铣削的次数:(来料规格 - 实际要求)/ 进力1间距
* 最终的铣削次数为 X 方向上的次数乘以 Y 方向上的次数。
3. 确定铣削顺序:根据铣削次数和机床的设定,确定铣削的起始位置和铣削顺序。通常,从最外边开始铣削,逐渐向内依次进行。
4. 执行铣削:按照计算得到的铣削次数和顺序,依次进行铣削操作。
根据您给出的示例数据,假设进力1间距为0.1mm,则计算方法如下:
X 方向上的需要铣削次数:(151.5 - 150) / 0.1 = 15
Y 方向上的需要铣削次数:(101.5 - 100) / 0.1 = 15
总的铣削次数:15 * 15 = 225
答案是:需要进行225次铣削操作。
对于我司内部的产品种类及产品构件在设计刀具磨头前我们首先要了解磨头的砂号及每个砂号所出现的砂边大小,写出目前我司内部的磨头砂号及对应的砂边:(例如:砂号:180#一砂边大小:1.5mm)答案是什么
亲,您好根据您的要求,我无法直接获取您司内部磨头砂号及对应的砂边信息,因为我无法访问特定公司的内部数据库或文件。这些信息通常是公司内部设计、制造或供应链部门根据产品需求和加工要求进行确定和管理的。
请把精雕机编程的流程方式写出来?
精雕机编程的基本流程包括以下几个步骤:
1. 了解加工要求
- 首先,您需要详细了解加工件的设计要求,包括尺寸、形状、加工工艺等。这将有助于确定合适的编程策略和刀具路径。
2. 创建CAD模型或准备工艺图纸
- 根据加工要求,您可以使用计算机辅助设计(CAD)软件创建三维模型,或者准备工艺图纸来描述加工件的几何形状和标注。
3. 选择CAM软件
- 使用计算机辅助制造(CAM)软件,将CAD模型或工艺图纸导入其中。CAM软件可以根据预设的加工参数生成刀具路径和编程代码。
4. 铣削策略选择
- 在CAM软件中,您需要选择合适的铣削策略,例如等高平面铣削、轮廓铣削、螺旋铣削等。根据加工要求和材料特性,选择合适的粗加工和精加工策略。
5. 工艺参数设置:
在CAM软件中,根据加工要求设置相关的工艺参数,如切削速度、进给速度、切削深度、切削宽度等。这些参数将影响加工过程的效率和质量。
6. 生成刀具路径:
基于所选择的铣削策略和工艺参数,CAM软件将生成刀具路径。这些路径描述了刀具在加工件上的运动轨迹和加工顺序。
7. 模拟和验证:
在将刀具路径下载到精雕机之前,您可以使用CAM软件提供的模拟功能来检查刀具路径的正确性,并验证加工过程中是否会出现干涉或其他问题。
8. 下载编程代码:
一旦刀具路径和加工参数确认无误,您可以将编程代码(通常是G代码或M代码)下载到精雕机控制系统中。
9. 设置工件和刀具:
在实际加工之前,您需要将工件安装到精雕机上,并安装选定的刀具。确保工件和刀具的位置和夹持方式正确。
10. 运行加工程序:
在精雕机上加载编程代码后,您可以执行加工程序。精雕机将按照编程代码中指定的路径和参数进行自动加工。在加工过程中,您可以监控加工过程,确保一切正常。