
模具设计要注意哪些事项,急用!!
3个回答
2019-03-01 · 农业农村部直属的大型综合出版社
关注
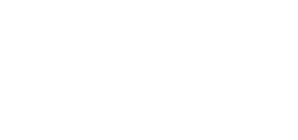
展开全部
无论使用何种模具都应注意模具要架设稳定,模接缝严密不漏浆,方便拆除。同时注意模具清洁,模板的几何形状支撑物要有足够的强度和刚度及稳定性罩洞清,考虑好进料口、出料口与拱盖或池墙模物前具的衔接。用砖做内模时应注意砖要内潮外颤瞎干。
2014-04-01
展开全部
模具设计注意事项⑴塑件形状及壁厚设计特别应考虑有利于料流畅通填充型腔,尽量避免尖角、缺口。⑵脱模斜度应取大,含玻璃纤维15%的可取1°~2°,含玻璃纤维30%的可取 2°~3°。当不允许碰慧有脱模斜度时则应避免强行脱模,宜采用横向分型结构。⑶浇注系统截面宜大,流程平直而短,以利于纤维均匀分散。⑷设计进料口应考虑防止填充不足,异向性变形,玻璃纤维分布不匀,易产生熔接痕等不良后果。进料口宜取薄片,宽薄,扇形,环形及多点形式进料口以使料流乱流,玻璃纤维均匀分散,以减少异向性,最好不采用针状进料口,进料口截面可适当增大,其长度应短。⑸模具型芯、型腔应有足够刚性及强度。⑹模具应淬硬,抛光、选用耐磨钢种,易磨损部位应便于修换。⑺顶出应均匀有力,便于换修。⑻模具应设有排气溢料槽,并宜设于易发生熔接痕部位。
模温的设定
⑴模温影响成型周期及成形品质,在实际操作当中是由使用材质的最低适当模温开始设定,然后根据品质状况来适当调高。
⑵正确的说法,模温是指在成形被进行时的模腔表面的温度,在模具设计及成形工程的条件设定上,重要的是不仅维持适当的温度,还要能让其均匀的分布。
⑶不均匀的模温分布,会导致不均匀的收缩和内应力,因而使成型口易发生变形和翘曲。
⑷提高模温可获得以下效果;①增加成形品结晶度及较均匀的结构。②使成型收缩较充分,后收缩减小。③提高成型品的强度和耐热性。④减少内应力残留、分子配向及变形。⑤减少充填时的流动阻抗,降低压力损失。⑥使成形品外观较具光泽。⑦增加成型品发生毛边的机会。⑧增加近浇口部位和减少远浇口部位凹陷的机会。⑨减少结合线明显的程度⑩增加冷却时间。
计量及可塑化⑴在成型加工法,射出量的控制(计量)以及塑料的均匀熔融(可塑化)是由射出机的可塑化机构(Plasticizing unit)来担春拆任的。①加热筒温度(Barrel Temperature)虽然塑料的熔融,大约有60--85%是因为螺杆的旋转所产生的热能,但是塑料的熔融状态仍然受加热筒温度的影响,尤以靠近喷嘴前区的温度--前区的温度过高时易发生滴料及取出制件时牵丝的现象。②螺杆转速(screw speed)A.塑料的熔融,大体是因螺杆的旋转所产生的热量,因此螺杆转速太快,则有下列影响:a.塑料的热分解。b.玻纤(加纤塑料)减短。c.螺杆或加热筒磨损加快。B.转速的设定,可以其圆周速的大小来衡量:圆周速=n(转速)*d(直径)*π(圆周率)通常,低粘度笑森答热安定性良好的塑料,其螺杆杆旋转的圆周速约可设定到 1m/s上下,但热安定性差的塑料,则应低到0.1左右。C.在实际应用当中,我们可以尽量调低螺杆转速,使旋转进料在开模前完成即可。③背压(BACK PRESSURE)A.当螺杆旋转进料时,推进到螺杆前端的熔胶所蓄积的压力称为背压,在射出成型时,可以由调整射出油压缸的退油压力来调节,背压可以有以下的效果:a.熔胶更均匀的熔解。b.色剂及填充物更加均匀的分散。c.使气体由落料口退出。d.进料的的计量准确。B.背压的高低,是依塑料的粘度及其热安定性来决定,太高的背压使进料时间延长,也因旋转剪切力的提高,容易使塑料产生过热。一般以5--15kg/cm2为宜。④松退(SUCK BACK,DECOMPRESSION)A.螺杆旋转进料开始前,使螺杆适当抽退,可以使模内前端熔胶压力降低,此称为前松退,其效果可防止喷嘴部的熔胶对螺杆的压力,多用于热流道模具的成型。B.螺杆旋转进料结束后,使螺杆适当抽退,可以使螺杆前端熔胶压力降低,此称为后松退,其效果可防止喷嘴部的滴料。C.不足之处,是容易使主流道(SPRUE)粘模;而太多的松退,则能吸进空气,使成型品发生气痕。
模温的设定
⑴模温影响成型周期及成形品质,在实际操作当中是由使用材质的最低适当模温开始设定,然后根据品质状况来适当调高。
⑵正确的说法,模温是指在成形被进行时的模腔表面的温度,在模具设计及成形工程的条件设定上,重要的是不仅维持适当的温度,还要能让其均匀的分布。
⑶不均匀的模温分布,会导致不均匀的收缩和内应力,因而使成型口易发生变形和翘曲。
⑷提高模温可获得以下效果;①增加成形品结晶度及较均匀的结构。②使成型收缩较充分,后收缩减小。③提高成型品的强度和耐热性。④减少内应力残留、分子配向及变形。⑤减少充填时的流动阻抗,降低压力损失。⑥使成形品外观较具光泽。⑦增加成型品发生毛边的机会。⑧增加近浇口部位和减少远浇口部位凹陷的机会。⑨减少结合线明显的程度⑩增加冷却时间。
计量及可塑化⑴在成型加工法,射出量的控制(计量)以及塑料的均匀熔融(可塑化)是由射出机的可塑化机构(Plasticizing unit)来担春拆任的。①加热筒温度(Barrel Temperature)虽然塑料的熔融,大约有60--85%是因为螺杆的旋转所产生的热能,但是塑料的熔融状态仍然受加热筒温度的影响,尤以靠近喷嘴前区的温度--前区的温度过高时易发生滴料及取出制件时牵丝的现象。②螺杆转速(screw speed)A.塑料的熔融,大体是因螺杆的旋转所产生的热量,因此螺杆转速太快,则有下列影响:a.塑料的热分解。b.玻纤(加纤塑料)减短。c.螺杆或加热筒磨损加快。B.转速的设定,可以其圆周速的大小来衡量:圆周速=n(转速)*d(直径)*π(圆周率)通常,低粘度笑森答热安定性良好的塑料,其螺杆杆旋转的圆周速约可设定到 1m/s上下,但热安定性差的塑料,则应低到0.1左右。C.在实际应用当中,我们可以尽量调低螺杆转速,使旋转进料在开模前完成即可。③背压(BACK PRESSURE)A.当螺杆旋转进料时,推进到螺杆前端的熔胶所蓄积的压力称为背压,在射出成型时,可以由调整射出油压缸的退油压力来调节,背压可以有以下的效果:a.熔胶更均匀的熔解。b.色剂及填充物更加均匀的分散。c.使气体由落料口退出。d.进料的的计量准确。B.背压的高低,是依塑料的粘度及其热安定性来决定,太高的背压使进料时间延长,也因旋转剪切力的提高,容易使塑料产生过热。一般以5--15kg/cm2为宜。④松退(SUCK BACK,DECOMPRESSION)A.螺杆旋转进料开始前,使螺杆适当抽退,可以使模内前端熔胶压力降低,此称为前松退,其效果可防止喷嘴部的熔胶对螺杆的压力,多用于热流道模具的成型。B.螺杆旋转进料结束后,使螺杆适当抽退,可以使螺杆前端熔胶压力降低,此称为后松退,其效果可防止喷嘴部的滴料。C.不足之处,是容易使主流道(SPRUE)粘模;而太多的松退,则能吸进空气,使成型品发生气痕。
本回答被提问者采纳
已赞过
已踩过<
评论
收起
你对这个回答的评价是?
展开全部
一、3D与2D分析
1、3D结构的分析。
2、2D图面公差、外观、材质分析。
二、开模方向和分型线
每个注塑产品在开始设计时首先要确定其开模方向和分型线,以保证尽可能减少抽芯滑块机构和消除分型线对外观的影响。
1、 开模方向确定后,产品的加强筋、卡扣、凸起等结构尽可能设计成与开模方向一致,以避免抽芯减少拼缝线,延长模具寿命。
2、 开模方向确定后,可选择适当的分型线,避免开模方向存在倒扣,以改善外观及性能。
三 、拔模角度
1 、适当的脱模斜度可避免产品拉毛(拉花)。光滑表面的脱模斜度应≥0.5度,细皮纹(砂面)表面大于2度,粗皮纹表面大于3度。
2 、适当的脱模斜度可避免产品顶伤,如顶白、顶变形、顶破。
3、 深腔结构产品设计时外表面斜度尽量要求大于内表面斜度,以保证注塑时模具型芯不偏位,得到均匀的产品壁厚,并保证产品开口部位的材料强度。
4、在进行做拔模的时候,注意2D图面公差尺寸的要求,拔模控制在公差范围以内。
四、 产品壁厚
1 、各种塑料均有一定的壁厚范围,一般0.5~4mm,当壁厚超过4mm时,将引起冷却时间过长,产生缩印等问题,应考虑改变产品结构。
2 、壁厚不均会引起表面缩水。
3 、壁厚不均会引起气孔和熔接痕。
4、产品壁厚不均匀的情况下,结构上需要做分化,防差拿止表面产品应力痕。
五、 加强筋
1、 加强筋的合理应用,可增加产品刚性,减少变形。
2、 加强筋的厚度必须≤ (0.5~0.7)T产品壁厚,否则引起表面缩水。
3、 加强筋的单面斜度应大于0.5°,以避免顶伤。
4、正常情况下,为了排气,加强筋在做镶件处理,如果加强筋高度在15MM以上的情况下,在镶件上面加强位,如果能用磨床加工的情况下,可以不做脱模斜度,但模仁一侧的斜度可以做大一点。
六、圆角
1、 圆角太小可能引起产品应力集中,导致产品开裂。
2、圆角太小可能引起模具型腔应力集中,导致型腔开裂。
3、 设置合理的圆角,还可以改善模具的加工工艺,如型腔可直接用R刀铣加工,而避免低效率的电加工。
4 、不同的圆角可能会引起分型线的移动,应结合实际情况选择不同的圆角或清角。
5、产品有装配变形的卡扣位区域时,根部可以追加0.2~0.3MM的R角,防止在装配过程中,卡扣断裂。
七、 孔
1 、孔的形状应尽量简单,一般取圆形。
2 、孔的轴向和开模方向一致,可以避免抽芯。
3 、当孔的长径比大于2时,应设置脱模斜度。此时孔的直径应按小径尺寸(最大实体尺寸)计算。
4 、盲孔的长径比超过10MM,的情况上,控制有效的装配与定位长度,其它的长度追加斜度来增加强度,而以尽量避免,进胶直接充填。
5 、孔与产品边缘的距离一般大于孔径尺寸,防止模具上存在尖铁与薄铁。
6、直径大于10MM的通孔情况下,最好做排气孔。
7、有孔的区域都会存在一个结合线,在条件允许的情况下,做镶件,增加气。
八、 注塑模的抽芯、滑块机构及避免
1、 当塑件按开模方向不能顺利脱模时,应设计抽芯滑块机构。抽芯机构滑块能成型复杂产品结构,但易引起产品拼缝线、缩水等缺陷,并增加模具成本缩短模具寿命。
2、设计注塑产品时,如无特虚庆雀殊要求,尽量避免抽芯结构。如孔轴向和筋的方向改为开模方向,利用型腔型芯碰穿等方法。
九、 嵌件
1 、在注塑产品中镶入嵌件可增加局部强度、硬度、尺寸精度和设置小螺纹孔(轴差早),满足各种特殊需求。同时会增加产品成本。
2 、嵌件一般为铜,也可以是其它金属或塑料件。
3 、嵌件在嵌入塑料中的部分应设计止转和防拔出结构。
如:滚花、孔、折弯、压扁、轴肩等。
4 、嵌件周围塑料应适当加厚,以防止塑件应力开裂。
5 、设计嵌件时,应充分考虑其在模具中的定位方式(孔、销、磁性)
十、 标识
1、产品标识一般设置在产品内表面较平坦处,并采用凸起形式,选择法向与开模方向尺可能一致的面处设置标识,可以避免拉伤。
2、年月章最好是独立,方便每年更换。
十一、 注塑件精度
由于注塑时收缩率的不均匀性和不确定性,注塑件精度明显低于金属件,不能简单地套用机械零件的尺寸公差应按标准选择适当的公差要求.我国也于1993年发布了GB/T14486-93 《工程塑料模塑塑料件尺寸公差》,设计者可根据所用的塑料原料和制件使用要求,根据标准中的规定确定制件的尺寸公差。
同时要根据工厂综合实力,同行的产品的设计精度来确定适合的设计公差精度。
十二、 注塑件的变形
1、提高注塑产品结构的刚性,减少变形。
2、尽量避免平板结构,合理设置翻边,凹凸结构。
3、设置合理的加强筋。
十三、扣位
1、将扣位装置设计成多个扣位同时共用,使整体的装置不会因为个别扣位的损坏而不能运作,从而增加其使用寿命,再是多考滤加圆角,增加强度。
2、是扣位相关尺寸的公差要求十分严谨,倒扣位置过多容易形成扣位损坏;相反,倒扣位置过少则装配位置难於控制或组合部份出现过松的现象。解决办法是要预留改模容易加胶的方式来实现。
十四、 焊接(热板焊、超声波焊、振动焊)
1、 采用焊接,可提高联接强度。
2 、采用焊接,可简化产品设计。
3、外观件超声波焊接的情况下,防止上下面的段差,以及超声波溢胶,设计时单边做好预留0.25MM以上平面。
十五、 合理考虑工艺和产品性能之间的矛盾
1 设计注塑产品时必须综合考虑产品外观、性能和工艺之间的矛盾。有时牺牲部分工艺性,可得到很好的外观或性能。
2 结构设计实在无法避免注塑缺陷时,尽可能让缺陷发生在产品的隐蔽部位。
十六、螺丝柱孔径与自攻螺丝直径的关系
自攻螺丝 螺丝柱孔径
M2 1.7mm
M2.3 2.0mm
M2.6 2.2mm
M3 2.5mm
十七、BOSS的设计原则:
1、 支柱尽量不要单独使用,应尽量连接至外壁或与加强筋一同使用,目的是加强支柱的强度及使胶料流动更顺畅。
2、 支柱高度一般是不会超过支柱直径的两倍半。因过高的支柱会导致塑胶部件成型时困气(长度太长的情况下,易变形,充填不满、在装配时易开裂)。
3、 支柱高度若超过支柱直径的两倍半,尤其是远离外壁的支柱,加强支柱的强度的方法是使用加强筋
4、 BOSS的形状以圆形为主﹐其它形状则加工不易
5、 BOSS的位置不能太接近转角或外侧壁,应与产品外壁保持一段距离
6、BOSS周围可用除去部分肉厚(即开火山口)来防收缩下陷
7、BOSS的拨模角度:外径尽量控制在0.5~1°,内径有效装配面尽量为零度。
1、3D结构的分析。
2、2D图面公差、外观、材质分析。
二、开模方向和分型线
每个注塑产品在开始设计时首先要确定其开模方向和分型线,以保证尽可能减少抽芯滑块机构和消除分型线对外观的影响。
1、 开模方向确定后,产品的加强筋、卡扣、凸起等结构尽可能设计成与开模方向一致,以避免抽芯减少拼缝线,延长模具寿命。
2、 开模方向确定后,可选择适当的分型线,避免开模方向存在倒扣,以改善外观及性能。
三 、拔模角度
1 、适当的脱模斜度可避免产品拉毛(拉花)。光滑表面的脱模斜度应≥0.5度,细皮纹(砂面)表面大于2度,粗皮纹表面大于3度。
2 、适当的脱模斜度可避免产品顶伤,如顶白、顶变形、顶破。
3、 深腔结构产品设计时外表面斜度尽量要求大于内表面斜度,以保证注塑时模具型芯不偏位,得到均匀的产品壁厚,并保证产品开口部位的材料强度。
4、在进行做拔模的时候,注意2D图面公差尺寸的要求,拔模控制在公差范围以内。
四、 产品壁厚
1 、各种塑料均有一定的壁厚范围,一般0.5~4mm,当壁厚超过4mm时,将引起冷却时间过长,产生缩印等问题,应考虑改变产品结构。
2 、壁厚不均会引起表面缩水。
3 、壁厚不均会引起气孔和熔接痕。
4、产品壁厚不均匀的情况下,结构上需要做分化,防差拿止表面产品应力痕。
五、 加强筋
1、 加强筋的合理应用,可增加产品刚性,减少变形。
2、 加强筋的厚度必须≤ (0.5~0.7)T产品壁厚,否则引起表面缩水。
3、 加强筋的单面斜度应大于0.5°,以避免顶伤。
4、正常情况下,为了排气,加强筋在做镶件处理,如果加强筋高度在15MM以上的情况下,在镶件上面加强位,如果能用磨床加工的情况下,可以不做脱模斜度,但模仁一侧的斜度可以做大一点。
六、圆角
1、 圆角太小可能引起产品应力集中,导致产品开裂。
2、圆角太小可能引起模具型腔应力集中,导致型腔开裂。
3、 设置合理的圆角,还可以改善模具的加工工艺,如型腔可直接用R刀铣加工,而避免低效率的电加工。
4 、不同的圆角可能会引起分型线的移动,应结合实际情况选择不同的圆角或清角。
5、产品有装配变形的卡扣位区域时,根部可以追加0.2~0.3MM的R角,防止在装配过程中,卡扣断裂。
七、 孔
1 、孔的形状应尽量简单,一般取圆形。
2 、孔的轴向和开模方向一致,可以避免抽芯。
3 、当孔的长径比大于2时,应设置脱模斜度。此时孔的直径应按小径尺寸(最大实体尺寸)计算。
4 、盲孔的长径比超过10MM,的情况上,控制有效的装配与定位长度,其它的长度追加斜度来增加强度,而以尽量避免,进胶直接充填。
5 、孔与产品边缘的距离一般大于孔径尺寸,防止模具上存在尖铁与薄铁。
6、直径大于10MM的通孔情况下,最好做排气孔。
7、有孔的区域都会存在一个结合线,在条件允许的情况下,做镶件,增加气。
八、 注塑模的抽芯、滑块机构及避免
1、 当塑件按开模方向不能顺利脱模时,应设计抽芯滑块机构。抽芯机构滑块能成型复杂产品结构,但易引起产品拼缝线、缩水等缺陷,并增加模具成本缩短模具寿命。
2、设计注塑产品时,如无特虚庆雀殊要求,尽量避免抽芯结构。如孔轴向和筋的方向改为开模方向,利用型腔型芯碰穿等方法。
九、 嵌件
1 、在注塑产品中镶入嵌件可增加局部强度、硬度、尺寸精度和设置小螺纹孔(轴差早),满足各种特殊需求。同时会增加产品成本。
2 、嵌件一般为铜,也可以是其它金属或塑料件。
3 、嵌件在嵌入塑料中的部分应设计止转和防拔出结构。
如:滚花、孔、折弯、压扁、轴肩等。
4 、嵌件周围塑料应适当加厚,以防止塑件应力开裂。
5 、设计嵌件时,应充分考虑其在模具中的定位方式(孔、销、磁性)
十、 标识
1、产品标识一般设置在产品内表面较平坦处,并采用凸起形式,选择法向与开模方向尺可能一致的面处设置标识,可以避免拉伤。
2、年月章最好是独立,方便每年更换。
十一、 注塑件精度
由于注塑时收缩率的不均匀性和不确定性,注塑件精度明显低于金属件,不能简单地套用机械零件的尺寸公差应按标准选择适当的公差要求.我国也于1993年发布了GB/T14486-93 《工程塑料模塑塑料件尺寸公差》,设计者可根据所用的塑料原料和制件使用要求,根据标准中的规定确定制件的尺寸公差。
同时要根据工厂综合实力,同行的产品的设计精度来确定适合的设计公差精度。
十二、 注塑件的变形
1、提高注塑产品结构的刚性,减少变形。
2、尽量避免平板结构,合理设置翻边,凹凸结构。
3、设置合理的加强筋。
十三、扣位
1、将扣位装置设计成多个扣位同时共用,使整体的装置不会因为个别扣位的损坏而不能运作,从而增加其使用寿命,再是多考滤加圆角,增加强度。
2、是扣位相关尺寸的公差要求十分严谨,倒扣位置过多容易形成扣位损坏;相反,倒扣位置过少则装配位置难於控制或组合部份出现过松的现象。解决办法是要预留改模容易加胶的方式来实现。
十四、 焊接(热板焊、超声波焊、振动焊)
1、 采用焊接,可提高联接强度。
2 、采用焊接,可简化产品设计。
3、外观件超声波焊接的情况下,防止上下面的段差,以及超声波溢胶,设计时单边做好预留0.25MM以上平面。
十五、 合理考虑工艺和产品性能之间的矛盾
1 设计注塑产品时必须综合考虑产品外观、性能和工艺之间的矛盾。有时牺牲部分工艺性,可得到很好的外观或性能。
2 结构设计实在无法避免注塑缺陷时,尽可能让缺陷发生在产品的隐蔽部位。
十六、螺丝柱孔径与自攻螺丝直径的关系
自攻螺丝 螺丝柱孔径
M2 1.7mm
M2.3 2.0mm
M2.6 2.2mm
M3 2.5mm
十七、BOSS的设计原则:
1、 支柱尽量不要单独使用,应尽量连接至外壁或与加强筋一同使用,目的是加强支柱的强度及使胶料流动更顺畅。
2、 支柱高度一般是不会超过支柱直径的两倍半。因过高的支柱会导致塑胶部件成型时困气(长度太长的情况下,易变形,充填不满、在装配时易开裂)。
3、 支柱高度若超过支柱直径的两倍半,尤其是远离外壁的支柱,加强支柱的强度的方法是使用加强筋
4、 BOSS的形状以圆形为主﹐其它形状则加工不易
5、 BOSS的位置不能太接近转角或外侧壁,应与产品外壁保持一段距离
6、BOSS周围可用除去部分肉厚(即开火山口)来防收缩下陷
7、BOSS的拨模角度:外径尽量控制在0.5~1°,内径有效装配面尽量为零度。
已赞过
已踩过<
评论
收起
你对这个回答的评价是?
推荐律师服务:
若未解决您的问题,请您详细描述您的问题,通过百度律临进行免费专业咨询