
电火花加工的工作原理是什么?
5个回答
展开全部
电火花加工的工作原理是:主要用于模具生产中的型孔、型腔加工,已成为模具制造业的主导加工方法,推动了模具行业的技术进步。
电火花加工具有如下特点:可以加工任何高强度、高硬度、高韧性、高脆性以及高纯度的导电材料;加工时无明显机械力,适用于低刚度工件和微细结构的加工。
脉冲参数可依据需要调节,可在同一台机床上进行粗加工、半精加工和精加工;电火花加工后的表面呈现的凹坑,有利于贮油和降低噪声;生产效率低于切削加工;放电过程有部分能量消耗在工具电极上,导致电极损耗,影响成形精度。
电火花加工的使用说明:
电火花加工能加工普通切削加工方法难以切削的材料和复杂形状工件;加工时无切削力;不产生毛刺和刀痕沟纹等缺陷;工具电极材料无须比工件材料硬;直接使用电能加工,便于实现自动化;加工后表面产生变质层,在某些应用中须进一步去除;工作液的净化和加工中产生的烟雾污染处理比较麻烦。
电火花加工的主要用于加工具有复杂形状的型孔和型腔的模具和零件;加工各种硬、脆材料,如硬质合金和淬火钢等;加工深细孔、异形孔、深槽、窄缝和切割薄片等;加工各种成形刀具、样板和螺纹环规等工具和量具。

2024-10-28 广告
牧野机床(中国)有限公司是一家领先的数控电火花机床制造商,总部位于江苏昆山。我们专注于高精密数控机床的研发与生产,产品涵盖多种型号的数控电火花加工机,以卓越的技术、高精度的加工能力和稳定的性能著称。牧野机床凭借丰富的行业经验和专业的技术团队...
点击进入详情页
本回答由数控加工中心提供
2018-04-13 · 工程机械属具,矿山机械设备、机床附件大全
关注
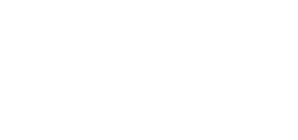
展开全部
进行电火花加工时,工具电极和工件分别接脉冲电源的两极,并浸入工作液中,或将工作液充入放电间隙。通过间隙自动控制系统控制工具电极向工件进给,当两电极间的间隙达到一定距离时,两电极上施加的脉冲电压将工作液击穿,产生火花放电。
在放电的微细通道中瞬时集中大量的热能,温度可高达一万摄氏度以上,压力也有急剧变化,从而使这一点工作表面局部微量的金属材料立刻熔化、气化,并爆炸式地飞溅到工作液中,迅速冷凝,形成固体的金属微粒,被工作液带走。这时在工件表面上便留下一个微小的凹坑痕迹,放电短暂停歇,两电极间工作液恢复绝缘状态。
紧接着,下一个脉冲电压又在两电极相对接近的另一点处击穿,产生火花放电,重复上述过程。这样,虽然每个脉冲放电蚀除的金属量极少,但因每秒有成千上万次脉冲放电作用,就能蚀除较多的金属,具有一定的生产率。在保持工具电极与工件之间恒定放电间隙的条件下,一边蚀除工件金属,一边使工具电极不断地向工件进给,最后便加工出与工具电极形状相对应的形状来。因此,只要改变工具电极的形状和工具电极与工件之间的相对运动方式,就能加工出各种复杂的型面。
工具电极常用导电性良好、熔点较高、易加工的耐电蚀材料,如铜、石墨、铜钨合金和钼等。在加工过程中,工具电极也有损耗,但小于工件金属的蚀除量,甚至接近于无损耗。
工作液作为放电介质,在加工过程中还起着冷却、排屑等作用。常用的工作液是粘度较低、闪点较高、性能稳定的介质,如煤油、去离子水和乳化液等。
在放电的微细通道中瞬时集中大量的热能,温度可高达一万摄氏度以上,压力也有急剧变化,从而使这一点工作表面局部微量的金属材料立刻熔化、气化,并爆炸式地飞溅到工作液中,迅速冷凝,形成固体的金属微粒,被工作液带走。这时在工件表面上便留下一个微小的凹坑痕迹,放电短暂停歇,两电极间工作液恢复绝缘状态。
紧接着,下一个脉冲电压又在两电极相对接近的另一点处击穿,产生火花放电,重复上述过程。这样,虽然每个脉冲放电蚀除的金属量极少,但因每秒有成千上万次脉冲放电作用,就能蚀除较多的金属,具有一定的生产率。在保持工具电极与工件之间恒定放电间隙的条件下,一边蚀除工件金属,一边使工具电极不断地向工件进给,最后便加工出与工具电极形状相对应的形状来。因此,只要改变工具电极的形状和工具电极与工件之间的相对运动方式,就能加工出各种复杂的型面。
工具电极常用导电性良好、熔点较高、易加工的耐电蚀材料,如铜、石墨、铜钨合金和钼等。在加工过程中,工具电极也有损耗,但小于工件金属的蚀除量,甚至接近于无损耗。
工作液作为放电介质,在加工过程中还起着冷却、排屑等作用。常用的工作液是粘度较低、闪点较高、性能稳定的介质,如煤油、去离子水和乳化液等。
本回答被网友采纳
已赞过
已踩过<
评论
收起
你对这个回答的评价是?
展开全部
已赞过
已踩过<
评论
收起
你对这个回答的评价是?
2022-07-24 · 百度认证:北京惠企网络技术有限公司官方账号
关注
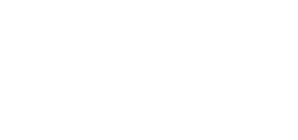
展开全部
其基本工作原理是利用连续移动的细金属丝(称为电极丝)作电极,对工件进行脉冲火花放电蚀除金属、切割成型。
线切割技术原理:
线切割加工是通过电火花的放电原理对零件进行加工。将工件接入脉冲电源正极,采用钼丝或铜丝作为切割金属丝,将金属丝接高频脉冲电源负极作为工具电极,利用火花放电对加工零件进行切割。
脉冲电源提供加工能量,加工过程中应用专用的线切割工作液清除加工中产生的碎屑。在电场的作用下,阴极和阳极表面分别受到电子流和离子流的轰击,使电极间隙内形成瞬时高温热源使局部金属熔化和气化。
气化后的工作液和工件材料蒸汽瞬间迅速膨胀,在这种热膨胀以及工作液冲压的共同作用下,熔化和气化的工件材料被抛出放电通道,至此完成一次火花放电过程。
线切割技术原理:
线切割加工是通过电火花的放电原理对零件进行加工。将工件接入脉冲电源正极,采用钼丝或铜丝作为切割金属丝,将金属丝接高频脉冲电源负极作为工具电极,利用火花放电对加工零件进行切割。
脉冲电源提供加工能量,加工过程中应用专用的线切割工作液清除加工中产生的碎屑。在电场的作用下,阴极和阳极表面分别受到电子流和离子流的轰击,使电极间隙内形成瞬时高温热源使局部金属熔化和气化。
气化后的工作液和工件材料蒸汽瞬间迅速膨胀,在这种热膨胀以及工作液冲压的共同作用下,熔化和气化的工件材料被抛出放电通道,至此完成一次火花放电过程。
已赞过
已踩过<
评论
收起
你对这个回答的评价是?
展开全部
电火花加工是利用浸在工作液中的两极间脉冲放电时产生的电蚀作用蚀除导电材料的特种加工方法,又称放电加工或电蚀加工,英文简称EDM。
1943年,苏联学者拉扎连科夫妇研究发明电火花加工,之后随着脉冲电源和控制系统的改进,而迅速发展起来。最初使用的脉冲电源是简单的电阻-电容回路。50年代初,改进为电阻-电感-电容等回路。同时,还采用脉冲发电机之类的所谓长脉冲电源,使蚀除效率提高,工具电极相对损耗降低。
随后又出现了大功率电子管、闸流管等高频脉冲电源,使在同样表面粗糙度条件下的生产率得以提高。60年代中期,出现了晶体管和可控硅脉冲电源,提高了能源利用效率和降低了工具电极损耗,并扩大了粗精加工的可调范围。
到70年代,出现了高低压复合脉冲、多回路脉冲、等幅脉冲和可调波形脉冲等电源,在加工表面粗糙度、加工精度和降低工具电极损耗等方面又有了新的进展。在控制系统方面,从最初简单地保持放电间隙,控制工具电极的进退,逐步发展到利用微型计算机,对电参数和非电参数等各种因素进行适时控制。
进行电火花加工时,工具电极和工件分别接脉冲电源的两极,并浸入工作液中,或将工作液充入放电间隙。通过间隙自动控制系统控制工具电极向工件进给,当两电极间的间隙达到一定距离时,两电极上施加的脉冲电压将工作液击穿,产生火花放电。
在放电的微细通道中瞬时集中大量的热能,温度可高达一万摄氏度以上,压力也有急剧变化,从而使这一点工作表面局部微量的金属材料立刻熔化、气化,并爆炸式地飞溅到工作液中,迅速冷凝,形成固体的金属微粒,被工作液带走。这时在工件表面上便留下一个微小的凹坑痕迹,放电短暂停歇,两电极间工作液恢复绝缘状态。
紧接着,下一个脉冲电压又在两电极相对接近的另一点处击穿,产生火花放电,重复上述过程。这样,虽然每个脉冲放电蚀除的金属量极少,但因每秒有成千上万次脉冲放电作用,就能蚀除较多的金属,具有一定的生产率。
在保持工具电极与工件之间恒定放电间隙的条件下,一边蚀除工件金属,一边使工具电极不断地向工件进给,最后便加工出与工具电极形状相对应的形状来。因此,只要改变工具电极的形状和工具电极与工件之间的相对运动方式,就能加工出各种复杂的型面。
工具电极常用导电性良好、熔点较高、易加工的耐电蚀材料,如铜、石墨、铜钨合金和钼等。在加工过程中,工具电极也有损耗,但小于工件金属的蚀除量,甚至接近于无损耗。
工作液作为放电介质,在加工过程中还起着冷却、排屑等作用。常用的工作液是粘度较低、闪点较高、性能稳定的介质,如煤油、去离子水和乳化液等。
按照工具电极的形式及其与工件之间相对运动的特征,可将电火花加工方式分为五类:利用成型工具电极,相对工件作简单进给运动的电火花成形加工;利用轴向移动的金属丝作工具电极,工件按所需形状和尺寸作轨迹运动,以切割导电材料的电火花线切割加工;利用金属丝或成形导电磨轮作工具电极,进行小孔磨削或成形磨削的电火花磨削;用于加工螺纹环规、螺纹塞规、齿轮等的电火花共轭回转加工;小孔加工、刻印、表面合金化、表面强化等其他种类的加工。
电火花加工能加工普通切削加工方法难以切削的材料和复杂形状工件;加工时无切削力;不产生毛刺和刀痕沟纹等缺陷;工具电极材料无须比工件材料硬;直接使用电能加工,便于实现自动化;加工后表面产生变质层,在某些应用中须进一步去除;工作液的净化和加工中产生的烟雾污染处理比较麻烦。
电火花加工的主要用于加工具有复杂形状的型孔和型腔的模具和零件;加工各种硬、脆材料,如硬质合金和淬火钢等;加工深细孔、异形孔、深槽、窄缝和切割薄片等;加工各种成形刀具、样板和螺纹环规等工具和量具。
1943年,苏联学者拉扎连科夫妇研究发明电火花加工,之后随着脉冲电源和控制系统的改进,而迅速发展起来。最初使用的脉冲电源是简单的电阻-电容回路。50年代初,改进为电阻-电感-电容等回路。同时,还采用脉冲发电机之类的所谓长脉冲电源,使蚀除效率提高,工具电极相对损耗降低。
随后又出现了大功率电子管、闸流管等高频脉冲电源,使在同样表面粗糙度条件下的生产率得以提高。60年代中期,出现了晶体管和可控硅脉冲电源,提高了能源利用效率和降低了工具电极损耗,并扩大了粗精加工的可调范围。
到70年代,出现了高低压复合脉冲、多回路脉冲、等幅脉冲和可调波形脉冲等电源,在加工表面粗糙度、加工精度和降低工具电极损耗等方面又有了新的进展。在控制系统方面,从最初简单地保持放电间隙,控制工具电极的进退,逐步发展到利用微型计算机,对电参数和非电参数等各种因素进行适时控制。
进行电火花加工时,工具电极和工件分别接脉冲电源的两极,并浸入工作液中,或将工作液充入放电间隙。通过间隙自动控制系统控制工具电极向工件进给,当两电极间的间隙达到一定距离时,两电极上施加的脉冲电压将工作液击穿,产生火花放电。
在放电的微细通道中瞬时集中大量的热能,温度可高达一万摄氏度以上,压力也有急剧变化,从而使这一点工作表面局部微量的金属材料立刻熔化、气化,并爆炸式地飞溅到工作液中,迅速冷凝,形成固体的金属微粒,被工作液带走。这时在工件表面上便留下一个微小的凹坑痕迹,放电短暂停歇,两电极间工作液恢复绝缘状态。
紧接着,下一个脉冲电压又在两电极相对接近的另一点处击穿,产生火花放电,重复上述过程。这样,虽然每个脉冲放电蚀除的金属量极少,但因每秒有成千上万次脉冲放电作用,就能蚀除较多的金属,具有一定的生产率。
在保持工具电极与工件之间恒定放电间隙的条件下,一边蚀除工件金属,一边使工具电极不断地向工件进给,最后便加工出与工具电极形状相对应的形状来。因此,只要改变工具电极的形状和工具电极与工件之间的相对运动方式,就能加工出各种复杂的型面。
工具电极常用导电性良好、熔点较高、易加工的耐电蚀材料,如铜、石墨、铜钨合金和钼等。在加工过程中,工具电极也有损耗,但小于工件金属的蚀除量,甚至接近于无损耗。
工作液作为放电介质,在加工过程中还起着冷却、排屑等作用。常用的工作液是粘度较低、闪点较高、性能稳定的介质,如煤油、去离子水和乳化液等。
按照工具电极的形式及其与工件之间相对运动的特征,可将电火花加工方式分为五类:利用成型工具电极,相对工件作简单进给运动的电火花成形加工;利用轴向移动的金属丝作工具电极,工件按所需形状和尺寸作轨迹运动,以切割导电材料的电火花线切割加工;利用金属丝或成形导电磨轮作工具电极,进行小孔磨削或成形磨削的电火花磨削;用于加工螺纹环规、螺纹塞规、齿轮等的电火花共轭回转加工;小孔加工、刻印、表面合金化、表面强化等其他种类的加工。
电火花加工能加工普通切削加工方法难以切削的材料和复杂形状工件;加工时无切削力;不产生毛刺和刀痕沟纹等缺陷;工具电极材料无须比工件材料硬;直接使用电能加工,便于实现自动化;加工后表面产生变质层,在某些应用中须进一步去除;工作液的净化和加工中产生的烟雾污染处理比较麻烦。
电火花加工的主要用于加工具有复杂形状的型孔和型腔的模具和零件;加工各种硬、脆材料,如硬质合金和淬火钢等;加工深细孔、异形孔、深槽、窄缝和切割薄片等;加工各种成形刀具、样板和螺纹环规等工具和量具。
本回答被网友采纳
已赞过
已踩过<
评论
收起
你对这个回答的评价是?
推荐律师服务:
若未解决您的问题,请您详细描述您的问题,通过百度律临进行免费专业咨询