
加工误差是什么,有哪些概念内容?
1个回答
2018-10-09 · 工程机械属具,矿山机械设备、机床附件大全
关注
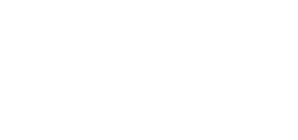
展开全部
加工误差是指被加工工件达到的实际几何参数(尺寸、形状和位置)对设计几何参数的偏离值。在生产实际中,影响加工精度的工艺因素是错综复杂的。对于某些加工误差问题,不能仅用单因素分析法来解决,而需要用概率统计方法进行综合分析,找出产生加工误差的原因,加以消除。
任何加工和测量都不可避免有误差存在,所谓精度较高,只是误差较小而已。加工误差是指零件加工后的实际几何参数(尺寸、几何形状和相互位置)与理想几何参数之间的偏差。加工误差的大小反映了加工精度的高低,生产中加工精度的高低,是用加工误差的大小来表示的。
零件的机械加工是在由机床、刀具、夹具和工件组成的工艺系统内完成的。因此,工艺系统各种误差就会以不同的程度和方式反映为零件的加工误差。
从错综复杂的生产中逐项分析产生加工误差的各项因素及其物理、力学本质,找出影响该项精度的主要因素,以便进一步采取措施去解决,该方法称为加工精度的单因素分析法。但在生产实际中,有时很难用单因素分析法来分析计算每一工序的加工误差,因为加工精度的影响因素比较复杂,是一个综合性很强的工艺问题,影响加工精度的原始误差很多,这些原始误差往往是综合地交错在一起对加工精度产生综合影响的,且其中不少原始误差的影响往往带有随机性。对于一个受多个随机性质原始误差影响的工艺系统,一般用概率统计的方法来进行综合分析,才能得出正确的、符合实际的结果。
加工误差的产生是由于在加工前和加工过程中,工艺系统存在很多误差因素,统称为原始误差。原始误差主要包括以下内容。
1、原理误差:采用近似的加工运动或近似的刀具轮廓而产生的误差。如用成形铣刀加工锥齿轮,用车削方法加工多边形工件等。
2、装夹误差:工件在装夹过程中产生的误差称为装夹误差。装夹误差包括定位误差和夹紧误差。
3、测量误差:测量误差是与量具、量仪的测量原理、制造精度、测量条件(温度、湿度、振动、测量力、清洁度等)以及测量技术水平等有关的误差。
4、调整误差:调整的作用主要是使刀具与工件之间达到正确的相对位置。试切法加工时的调整误差主要取决于测量误差、机床的进给误差和工艺系统的受力变形。调整法加工时的调整误差,除上述因素外,还与调整方法有关。采用定程机构调整时,与行程挡块、靠模、凸轮等元件或机构的制造误差、安装误差、磨损以及电、液、气控制元件的工作性能有关。采用样板、样件、对刀块、导套等调整,则与它们的制造、安装误差、磨损以及调整时的测量误差有关。
5、夹具的制造、安装误差与磨损:机床夹具上定位元件、导向元件、对刀元件、分度机构、夹具体等的加工与装配误差以及它们的耐磨损性能,对零件的加工精度有直接影响。夹具的精度要求,应根据工件的加工精度要求确定。
6、刀具的制造误差与磨损:刀具对加工精度的影响,随刀具种类的不同而不同。
7、工件误差:加工前,工件或毛坯上待加工表面本身有形状误差或与其有关表面有位置误差,也都会造成加工后该表面本身及与其有关表面的加工误差。
8、机床误差:机床的制造、安装误差以及长期使用后的磨损是造成加工误差的主要原始误差因素。机床误差主要由主轴回转误差、导轨导向误差、内传动链的传动误差及主轴、导轨等的位置关系误差所组成。
9、工艺系统受力变形产生的误差:工艺系统在切削力、传动力、重力、惯性力等外力作用下产生变形,破坏了刀具与工件间的正确相对位置,造成加工误差。工艺系统变形的大小与工艺系统的刚度有关。
10、工艺系统受热变形引起的误差:机械加工中,工艺系统受切削热、摩擦热、环境温度、辐射热等的影响将产生变形,使T件和刀具的正确相对位置遭到破坏,引起切削运动、背吃刀量及切削力的变化,造成加工误差。
11、工件残余应力引起的误差:在没有外力作用下或去除外力后,工件内仍存留的力称残余应力。具有残余应力的零件,其内部组织的平衡状态极不稳定,有恢复到无应力状态的强烈倾向。
任何加工和测量都不可避免有误差存在,所谓精度较高,只是误差较小而已。加工误差是指零件加工后的实际几何参数(尺寸、几何形状和相互位置)与理想几何参数之间的偏差。加工误差的大小反映了加工精度的高低,生产中加工精度的高低,是用加工误差的大小来表示的。
零件的机械加工是在由机床、刀具、夹具和工件组成的工艺系统内完成的。因此,工艺系统各种误差就会以不同的程度和方式反映为零件的加工误差。
从错综复杂的生产中逐项分析产生加工误差的各项因素及其物理、力学本质,找出影响该项精度的主要因素,以便进一步采取措施去解决,该方法称为加工精度的单因素分析法。但在生产实际中,有时很难用单因素分析法来分析计算每一工序的加工误差,因为加工精度的影响因素比较复杂,是一个综合性很强的工艺问题,影响加工精度的原始误差很多,这些原始误差往往是综合地交错在一起对加工精度产生综合影响的,且其中不少原始误差的影响往往带有随机性。对于一个受多个随机性质原始误差影响的工艺系统,一般用概率统计的方法来进行综合分析,才能得出正确的、符合实际的结果。
加工误差的产生是由于在加工前和加工过程中,工艺系统存在很多误差因素,统称为原始误差。原始误差主要包括以下内容。
1、原理误差:采用近似的加工运动或近似的刀具轮廓而产生的误差。如用成形铣刀加工锥齿轮,用车削方法加工多边形工件等。
2、装夹误差:工件在装夹过程中产生的误差称为装夹误差。装夹误差包括定位误差和夹紧误差。
3、测量误差:测量误差是与量具、量仪的测量原理、制造精度、测量条件(温度、湿度、振动、测量力、清洁度等)以及测量技术水平等有关的误差。
4、调整误差:调整的作用主要是使刀具与工件之间达到正确的相对位置。试切法加工时的调整误差主要取决于测量误差、机床的进给误差和工艺系统的受力变形。调整法加工时的调整误差,除上述因素外,还与调整方法有关。采用定程机构调整时,与行程挡块、靠模、凸轮等元件或机构的制造误差、安装误差、磨损以及电、液、气控制元件的工作性能有关。采用样板、样件、对刀块、导套等调整,则与它们的制造、安装误差、磨损以及调整时的测量误差有关。
5、夹具的制造、安装误差与磨损:机床夹具上定位元件、导向元件、对刀元件、分度机构、夹具体等的加工与装配误差以及它们的耐磨损性能,对零件的加工精度有直接影响。夹具的精度要求,应根据工件的加工精度要求确定。
6、刀具的制造误差与磨损:刀具对加工精度的影响,随刀具种类的不同而不同。
7、工件误差:加工前,工件或毛坯上待加工表面本身有形状误差或与其有关表面有位置误差,也都会造成加工后该表面本身及与其有关表面的加工误差。
8、机床误差:机床的制造、安装误差以及长期使用后的磨损是造成加工误差的主要原始误差因素。机床误差主要由主轴回转误差、导轨导向误差、内传动链的传动误差及主轴、导轨等的位置关系误差所组成。
9、工艺系统受力变形产生的误差:工艺系统在切削力、传动力、重力、惯性力等外力作用下产生变形,破坏了刀具与工件间的正确相对位置,造成加工误差。工艺系统变形的大小与工艺系统的刚度有关。
10、工艺系统受热变形引起的误差:机械加工中,工艺系统受切削热、摩擦热、环境温度、辐射热等的影响将产生变形,使T件和刀具的正确相对位置遭到破坏,引起切削运动、背吃刀量及切削力的变化,造成加工误差。
11、工件残余应力引起的误差:在没有外力作用下或去除外力后,工件内仍存留的力称残余应力。具有残余应力的零件,其内部组织的平衡状态极不稳定,有恢复到无应力状态的强烈倾向。
推荐律师服务:
若未解决您的问题,请您详细描述您的问题,通过百度律临进行免费专业咨询