
数控车床加工尺寸精度的误差原因都有哪些
1个回答
2018-01-28 · 工程机械属具,矿山机械设备、机床附件大全
关注
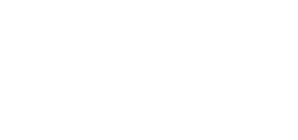
展开全部
尺寸精度是指加工后的工件尺寸和图纸尺寸要求相符合的程度。两者不相符合的程度通常是用误差大小来衡量。误差包括加工误差、安装误差和定位误差。其中,后两种误差是与工件和刀具的定位、安装有关,和加工本身无关。要提高加工精度减小加工误差,首先要选择高精度的机床,保证工件和刀具的安装定位精度,其次主要与数控车床加工工艺有关。
工艺系统中的各组成部分,包括机床、刀具、夹具的制造误差、安装误差、使用中的磨损都直接影响工件的加工精度。也就是说,在加工过程中工艺系统会产生各种误差,从而改变刀具和工件在切削运动过程中的相互位置关系而影响零件的加工精度。数控车床加工认准钛浩机械,专业品质保障,这些误差与工艺系统本身的结构状态和切削过程有关,产生加工误差的主要因素有:
1、加工原理误差
加工原理误差是由于采用了近似的加工运动方式或者近似的刀具轮廓而产生的误差,因在加工原理上存在误差,故称加工原理误差。只要原理误差在允许范围内,这种加工方式仍是可行的。
2、机床的几何误差
机床的制造误差、安装误差以及使用中的磨损,都直接影响工件的加工精度。其中主要是机床主轴回转运动、机床导轨直线运动和机床传动链的误差。
3、刀具的制造误差及弹性变形
我们很多人都有这样的经历,就是在前一刀车削了几毫米切深以后,发现离想要的尺寸还差几丝或者十几丝时,再按计划进行下一刀切削时,发现多切了很多,尺寸可能超差了。那么这样的情况我们认真分析过其中的原因吗?有人说,这可能是因为机床间隙比较大所致,而在同一进刀方向上是不会受间隙影响的,其真正原因就是弹性形变和弹性恢复。
弹性形变表现在刀具、机床丝杠副、刀架、加工零件本身等对象的形变,使刀具相对工件出现后退,阻力减小时形变恢复又会出现过切,使工件报废。产生形变的最终原因是这些对象的强度不足和切削力太大。
弹性形变会直接影响零件加工尺寸精度,有时还会影响几何精度(如零件变形时容易产生锥度,因为远离卡盘的位置形变幅度越大),刀具的强度不足,我们可以设法提高,有时机床和零件本身的强度,我们是没法选择或改变的,所以我们只能从减小切削力方面着手,来设法克服弹性形变,切深越小、刀具越锋利、工件材料硬度较低、走刀速度减小等都会减小实际切削阻力,都会减轻弹性形变。
所以为了保证工件的尺寸精度,我们往往把精加工、半精加工和粗加工分开,也就是说把弹性形变大的和弹性形变小的不同工序分开进行(粗加工时追求效率基本不追求精度,刀具需要偏钝,侧重强度,精加工时切削量很小,追求精度,刀具侧重锋利,减小切削阻力),在对刀试切时,就按照不同工序实际加工时的切深进行试切,确保试切时和实际加工时阻力和弹性形变幅度大致相当,确保数控机床坐标系建立准确,确保普通机床进刀准确;然后在精加工时尽可能采用比较锋利的刀具,最大程度减小切削抗力、减小形变。
刀具的制造误差、安装误差以及使用中的磨损,都影响工件的加工精度。刀具在切削过程中,切削刃、刀面与工件、切屑产生强烈摩擦,使刀具磨损。当刀具磨损达到一定值时,工件的表面粗糙度值增大,切屑颜色和形状发生变化,并伴有振动。刀具磨损将直接影响切削生产率、加工质量和成本。
4、夹具误差
夹具误差包括定位误差、夹紧误差、夹具安装误差及对刀误差等,这些误差主要与夹具的制造和装配精度有关。
4.1、基准不重合误差
当定位基准与工序基准不重合时而造成的加工误差,称为基准不重合误差,其大小等于定位基准与工序基准之间尺寸的公差。
4.2、基准位移误差
工件在夹具中定位时,由于工件定位基面与夹具上定位元件限位基面的制造公差和最小配合间隙的影响,导致定位基准与限位基准不能重合,从而使各个工件的位置不一致,给加工尺寸造成误差,这个误差称为基准位移误差。
5、转速对加工的影响
正常情况下,大家知道,转速越高,切削的效率越高,效率就是利润,所以,我们要在条件允许的情况下,运行尽可能高的转速进行切削。但转速、工件直径确定切削线速度,线速度受工件硬度、强度、塑性、含碳量、含难切削合金量和刀具的硬度及几何性能等因素制约,所以要在线速度限制下选择尽可能高的转速。另外转速高低选择要根据不同材质的刀具确定,例如高速钢加工钢件时,转速较低时粗糙度较好,而硬质合金刀具则转速较高时,粗糙度较好。再者,在加工细长轴或薄壁件时,要注意将转速调整避开零件共振区,防止产生振纹影响表面粗糙度。
6、切削要素对表面粗糙度的影响
我们知道工件材质较硬时,加工后工件表面粗糙度较好,另外当工件材料的可塑性和延展性越高时(如铜材、铝材),就需要刀具越锋利才能加工出比较好的表面粗糙度,灰铸铁加工相对于钢件加工来说,因为成份复杂,含杂质程度高,就需要刀具硬度较高。有些延展性较高强度又较高的合金材料,就需要锋利却又能保证强度的刀具,所以就比较难加工(如不锈钢、镍基耐热合金、钛合金等)。
除了材料对刀具提出要求以外,切削要素对表面粗糙度也会产生影响,当精加工切深太小,甚至比刀具刃厚还小时,刀刃已不能实现正常切削,所以产生挤压,也就会出现很差的表面粗糙度。当切深太大,甚至使刀具产生弯曲时,这时工件材料是被撕裂下来的,所以在工件上会留下很多丝状铁屑残留和较明显的纹路。走刀速度对工件表面粗糙度的影响也是相当明显的,当走刀速度加快或刀具副偏角不恰当时,会使走刀纹路高度加大,也就使表面粗糙度变差。
刀具不是很锋利的情况下,切深太小,甚至比刀刃厚度还小时,已经不是正常的切削了,只能属于“刮”或“研”,所加工工件表面粗糙度会下降,工件表面出现细微白丝,好像笼罩一层白雾,所以要注意控制。
工艺系统中的各组成部分,包括机床、刀具、夹具的制造误差、安装误差、使用中的磨损都直接影响工件的加工精度。也就是说,在加工过程中工艺系统会产生各种误差,从而改变刀具和工件在切削运动过程中的相互位置关系而影响零件的加工精度。数控车床加工认准钛浩机械,专业品质保障,这些误差与工艺系统本身的结构状态和切削过程有关,产生加工误差的主要因素有:
1、加工原理误差
加工原理误差是由于采用了近似的加工运动方式或者近似的刀具轮廓而产生的误差,因在加工原理上存在误差,故称加工原理误差。只要原理误差在允许范围内,这种加工方式仍是可行的。
2、机床的几何误差
机床的制造误差、安装误差以及使用中的磨损,都直接影响工件的加工精度。其中主要是机床主轴回转运动、机床导轨直线运动和机床传动链的误差。
3、刀具的制造误差及弹性变形
我们很多人都有这样的经历,就是在前一刀车削了几毫米切深以后,发现离想要的尺寸还差几丝或者十几丝时,再按计划进行下一刀切削时,发现多切了很多,尺寸可能超差了。那么这样的情况我们认真分析过其中的原因吗?有人说,这可能是因为机床间隙比较大所致,而在同一进刀方向上是不会受间隙影响的,其真正原因就是弹性形变和弹性恢复。
弹性形变表现在刀具、机床丝杠副、刀架、加工零件本身等对象的形变,使刀具相对工件出现后退,阻力减小时形变恢复又会出现过切,使工件报废。产生形变的最终原因是这些对象的强度不足和切削力太大。
弹性形变会直接影响零件加工尺寸精度,有时还会影响几何精度(如零件变形时容易产生锥度,因为远离卡盘的位置形变幅度越大),刀具的强度不足,我们可以设法提高,有时机床和零件本身的强度,我们是没法选择或改变的,所以我们只能从减小切削力方面着手,来设法克服弹性形变,切深越小、刀具越锋利、工件材料硬度较低、走刀速度减小等都会减小实际切削阻力,都会减轻弹性形变。
所以为了保证工件的尺寸精度,我们往往把精加工、半精加工和粗加工分开,也就是说把弹性形变大的和弹性形变小的不同工序分开进行(粗加工时追求效率基本不追求精度,刀具需要偏钝,侧重强度,精加工时切削量很小,追求精度,刀具侧重锋利,减小切削阻力),在对刀试切时,就按照不同工序实际加工时的切深进行试切,确保试切时和实际加工时阻力和弹性形变幅度大致相当,确保数控机床坐标系建立准确,确保普通机床进刀准确;然后在精加工时尽可能采用比较锋利的刀具,最大程度减小切削抗力、减小形变。
刀具的制造误差、安装误差以及使用中的磨损,都影响工件的加工精度。刀具在切削过程中,切削刃、刀面与工件、切屑产生强烈摩擦,使刀具磨损。当刀具磨损达到一定值时,工件的表面粗糙度值增大,切屑颜色和形状发生变化,并伴有振动。刀具磨损将直接影响切削生产率、加工质量和成本。
4、夹具误差
夹具误差包括定位误差、夹紧误差、夹具安装误差及对刀误差等,这些误差主要与夹具的制造和装配精度有关。
4.1、基准不重合误差
当定位基准与工序基准不重合时而造成的加工误差,称为基准不重合误差,其大小等于定位基准与工序基准之间尺寸的公差。
4.2、基准位移误差
工件在夹具中定位时,由于工件定位基面与夹具上定位元件限位基面的制造公差和最小配合间隙的影响,导致定位基准与限位基准不能重合,从而使各个工件的位置不一致,给加工尺寸造成误差,这个误差称为基准位移误差。
5、转速对加工的影响
正常情况下,大家知道,转速越高,切削的效率越高,效率就是利润,所以,我们要在条件允许的情况下,运行尽可能高的转速进行切削。但转速、工件直径确定切削线速度,线速度受工件硬度、强度、塑性、含碳量、含难切削合金量和刀具的硬度及几何性能等因素制约,所以要在线速度限制下选择尽可能高的转速。另外转速高低选择要根据不同材质的刀具确定,例如高速钢加工钢件时,转速较低时粗糙度较好,而硬质合金刀具则转速较高时,粗糙度较好。再者,在加工细长轴或薄壁件时,要注意将转速调整避开零件共振区,防止产生振纹影响表面粗糙度。
6、切削要素对表面粗糙度的影响
我们知道工件材质较硬时,加工后工件表面粗糙度较好,另外当工件材料的可塑性和延展性越高时(如铜材、铝材),就需要刀具越锋利才能加工出比较好的表面粗糙度,灰铸铁加工相对于钢件加工来说,因为成份复杂,含杂质程度高,就需要刀具硬度较高。有些延展性较高强度又较高的合金材料,就需要锋利却又能保证强度的刀具,所以就比较难加工(如不锈钢、镍基耐热合金、钛合金等)。
除了材料对刀具提出要求以外,切削要素对表面粗糙度也会产生影响,当精加工切深太小,甚至比刀具刃厚还小时,刀刃已不能实现正常切削,所以产生挤压,也就会出现很差的表面粗糙度。当切深太大,甚至使刀具产生弯曲时,这时工件材料是被撕裂下来的,所以在工件上会留下很多丝状铁屑残留和较明显的纹路。走刀速度对工件表面粗糙度的影响也是相当明显的,当走刀速度加快或刀具副偏角不恰当时,会使走刀纹路高度加大,也就使表面粗糙度变差。
刀具不是很锋利的情况下,切深太小,甚至比刀刃厚度还小时,已经不是正常的切削了,只能属于“刮”或“研”,所加工工件表面粗糙度会下降,工件表面出现细微白丝,好像笼罩一层白雾,所以要注意控制。
推荐律师服务:
若未解决您的问题,请您详细描述您的问题,通过百度律临进行免费专业咨询
广告 您可能关注的内容 |