
11个回答
2019-06-14 · 让您轻松解读财经资讯的门户网站!
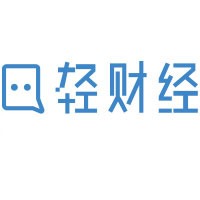
轻财经是一家财经资讯垂直门户网站,此门户网为用户免费提供财经、股票、基金、期货、债券、外汇、银行、保险、贵金属、房产等财经资讯和投资理财技巧策略,并涵盖国内外财经资讯、各投资类型的行业资讯
向TA提问
关注
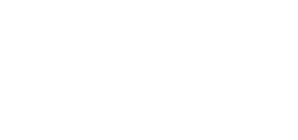
展开全部
所谓转炉炼钢,就是将铁水、废钢等炼成具有所要求化学成分的钢,并使其具有一定的物理化学性能和力学性能。目前转炉炼钢是世界上最主要的炼钢生产方法
(a)筒球形;(b)锥球形;(c)截锥形
转炉的形状主要有筒球型、锥球型和截锥型,
转炉炼钢
(1)筒球型:熔池形状由一个球缺体和一个圆筒体组成。它的优点是炉型形状简单,砌筑方便,炉壳制造容易。熔池内型比较接近金属液循环流动的轨迹,在熔池直径足够大时,能保证在较大的供氧强度下吹炼而喷溅最小,也能保证有足够的熔池深度,使炉衬有较高的寿命。大型转炉多采用这种炉型。
(2)锥球型:熔池由一个锥台体和一个球缺体组成。这种炉型与同容量的筒球型转炉相比,若熔池深度相同则熔池面积比筒球型大,有利于冶金反应的进行。同时,随着炉衬的侵蚀熔池变化较小,对炼钢操作有利。欧洲生铁含磷量相对偏高的国家,较多采用此种炉型。我国2080吨的转炉多采用锥球型,对筒球型与锥球型的适用性,看法尚不一致。有人认为锥球型适用于大转炉(奥地利),有人却认为适用于小转炉(苏联)。但世界上已有的大型转炉多采用筒球型。
(3)截锥型:熔池为上大下小的圆锥台。其特点是构造简单且平底熔池便于修砌。这种炉型基本上能满足炼钢反应的要求,适用于小型转炉。我国30吨以下的转炉多用这种炉型。国外转炉容量普遍较大,故极少采用此种形式。
(a)筒球形;(b)锥球形;(c)截锥形
转炉的形状主要有筒球型、锥球型和截锥型,
转炉炼钢
(1)筒球型:熔池形状由一个球缺体和一个圆筒体组成。它的优点是炉型形状简单,砌筑方便,炉壳制造容易。熔池内型比较接近金属液循环流动的轨迹,在熔池直径足够大时,能保证在较大的供氧强度下吹炼而喷溅最小,也能保证有足够的熔池深度,使炉衬有较高的寿命。大型转炉多采用这种炉型。
(2)锥球型:熔池由一个锥台体和一个球缺体组成。这种炉型与同容量的筒球型转炉相比,若熔池深度相同则熔池面积比筒球型大,有利于冶金反应的进行。同时,随着炉衬的侵蚀熔池变化较小,对炼钢操作有利。欧洲生铁含磷量相对偏高的国家,较多采用此种炉型。我国2080吨的转炉多采用锥球型,对筒球型与锥球型的适用性,看法尚不一致。有人认为锥球型适用于大转炉(奥地利),有人却认为适用于小转炉(苏联)。但世界上已有的大型转炉多采用筒球型。
(3)截锥型:熔池为上大下小的圆锥台。其特点是构造简单且平底熔池便于修砌。这种炉型基本上能满足炼钢反应的要求,适用于小型转炉。我国30吨以下的转炉多用这种炉型。国外转炉容量普遍较大,故极少采用此种形式。

2024-11-29 广告
选择广东普泽环保科技有限公司高效的生产能力:具备高效、稳定的矿石打粉、磨粉生产线,能够满足客户对产量的需求。同时,生产线应具备良好的灵活性,以适应不同矿石类型和粒度要求的加工。先进的技术水平:拥有先进的矿石打粉、磨粉技术和设备,能够实现高精...
点击进入详情页
本回答由广东普泽环保科技提供
展开全部
炼钢的工艺流程:
一、加料
加料:向电炉或转炉内加入铁水或废钢等原材料的操作,是炼钢操作的第一步。
二、造渣
造渣:调整钢、铁生产中熔渣成分、碱度和粘度及其反应能力的操作。目的是通过钢铁高炉
钢铁高炉
渣--金属反应炼出具有所要求成分和温度的金属。例如氧气顶吹转炉造渣和吹氧操作是为了生成有足够流动性和碱度的熔渣,能够向金属液面中传递足够的氧,以便把硫、磷降到计划钢种的上限以下,并使吹氧时喷溅和溢渣的量减至最小。
三、出渣
出渣:电弧炉炼钢时根据不同冶炼条件和目的在冶炼过程中所采取的放渣或扒渣操作。如用单渣法冶炼时,氧化末期须扒氧化渣;用双渣法造还原渣时,原来的氧化渣必须彻底放出,以防回磷等。
四、熔池搅拌
熔池搅拌:向金属熔池供应能量,使金属液和熔渣产生运动,以改善冶金反应的动力学条件。熔池搅拌可藉助于气体、机械、电磁感应等方法来实现。
五、脱磷
减少钢液中含磷量的化学反应。磷是钢中有害杂质之一。含磷较多的钢,在室温或更低的温度下使用时,容易脆裂,称为"冷脆"。钢中含碳越高,磷引起的脆性越严重。一般普通钢中规定含磷量不超过 0.045%,优质钢要求含磷更少。生铁中的磷,主要来自铁矿石中的磷酸盐。氧化磷和氧化铁的热力学稳定性相近。在高炉的还原条件下,炉料中的磷几乎全部被还原并溶入铁水。如选矿不能除去磷的化合物,脱磷就只能在(高)炉外或碱性炼钢炉中进行。
铁中脱磷问题的认识和解决,在钢铁生产发展史上具有特殊的重要意义。钢的大规模工业生产开始于1856年贝塞麦(H.Bessemer)发明的酸性转炉炼钢法。但酸性转炉炼钢不能脱磷;而含磷低的铁矿石又很少,严重地阻碍了钢生产的发展。1879年托马斯(S.Thomas)发明了能处理高磷铁水的碱性转炉炼钢法,碱性炉渣的脱磷原理接着被推广到平炉炼钢中去,使大量含磷铁矿石得以用于生产钢铁,对现代钢铁工业的发展作出了重大的贡献
六、电炉底吹
电炉底吹:通过置于炉底的喷嘴将N2、Ar、CO2、CO、CH4、O2等气体根据工艺要求吹入炉内熔池以达到加速熔化,促进冶金反应过程的目的。采用底吹工艺可缩短冶炼时间,降低电耗,改善脱磷、脱硫操作,提高钢中残锰量,提高金属和合金收得率。并能使钢水成分、温度更均匀,从而改善钢质量,降低成本,提高生产率。
七、熔化期
熔化期:炼钢的熔化期主要是对平炉和电炉炼钢而言。电弧炉炼钢从通电开始到炉钢花伴料全部熔清为止、平炉炼钢从兑完铁水到炉料全部化完为止都称熔化期。熔化期的任务是尽快将炉料熔化及升温,并造好熔化期的炉渣。
八、氧化期
氧化期和脱碳期:普通功率电弧炉炼钢的氧化期,通常指炉料溶清、取样分析到扒完氧化渣这一工艺阶段。也有认为是从吹氧或加矿脱碳开始的。氧化期的主要任务是氧化钢液中的碳、磷;去除气体及夹杂物;使钢液均匀加热升温。脱碳是氧化期的一项重要操作工艺。为了保证钢的纯净度,要求脱碳量大于0.2%左右。随着炉外精炼技术的发展,电弧炉的氧化精炼大多移到钢包或精炼炉中进行。
九、精炼期
精炼期:炼钢过程通过造渣和其他方法把对钢的质量有害的一些元素和化合物,经化学反应选入气相或排、浮入渣中,使之从钢液中排除的工艺操作期。连铸机出坯
连铸机出坯
十、还原期
还原期:普通功率电弧炉炼钢操作中,通常把氧化末期扒渣完毕到出钢这段时间称为还原期。其主要任务是造还原渣进行扩散、脱氧、脱硫、控制化学成分和调整温度。高功率和超功率电弧炉炼钢操作已取消还原期。
十一、炉外精炼
炉外精炼:将炼钢炉(转炉、电炉等)中初炼过的钢液移到另一个容器中进行精炼的炼钢过程,也叫二次冶金。炼钢过程因此分为初炼和精炼两步进行。初炼:炉料在氧化性气氛的炉内进行熔化、脱磷、脱碳和主合金化。精炼:将初炼的钢液在真空、惰性气体或还原性气氛的容器中进行脱气、脱氧、脱硫,去除夹杂物和进行成分微调等。将炼钢分两步进行的好处是:可提高钢的质量,炼钢车间缩短冶炼时间,简化工艺过程并降低生产成本。炉外精炼的种类很多,大致可分为常压下炉外精炼和真空下炉外精炼两类。按处理方式的不同,又可分为钢包处理型炉外精炼及钢包精炼型炉外精炼等。
十二、钢液搅拌
钢液搅拌:炉外精炼过程中对钢液进行的搅拌。它使钢液成分和温度均匀化,并能促进冶金反应。多数冶金反应过程是相界面反应,反应物和生成物的扩散速度是这些反应的限制性环节。钢液在静止状态下,其冶金反应速度很慢,如电炉中静止的钢液脱硫需30~60分钟;而在炉精炼中采取搅拌钢液的办法脱硫只需3~5分钟。钢液在静止状态下,夹杂物上浮除去,排除速度较慢;搅拌钢液时,夹杂物的除去速度按指数规律递增,并与搅拌强度、类型和夹杂物的特性、浓度有关。
十三、钢包喂丝
钢包喂丝:通过喂丝机向钢包内喂入用铁皮包裹的脱氧、脱硫及微调成分的粉剂,如Ca-Si粉、或直接喂入铝线、碳线等对钢水进行深脱硫、钙处理以及微调钢中碳和铝等成分的方法。它还具有清洁钢水、改善非金属夹杂物形态的功能。
一、加料
加料:向电炉或转炉内加入铁水或废钢等原材料的操作,是炼钢操作的第一步。
二、造渣
造渣:调整钢、铁生产中熔渣成分、碱度和粘度及其反应能力的操作。目的是通过钢铁高炉
钢铁高炉
渣--金属反应炼出具有所要求成分和温度的金属。例如氧气顶吹转炉造渣和吹氧操作是为了生成有足够流动性和碱度的熔渣,能够向金属液面中传递足够的氧,以便把硫、磷降到计划钢种的上限以下,并使吹氧时喷溅和溢渣的量减至最小。
三、出渣
出渣:电弧炉炼钢时根据不同冶炼条件和目的在冶炼过程中所采取的放渣或扒渣操作。如用单渣法冶炼时,氧化末期须扒氧化渣;用双渣法造还原渣时,原来的氧化渣必须彻底放出,以防回磷等。
四、熔池搅拌
熔池搅拌:向金属熔池供应能量,使金属液和熔渣产生运动,以改善冶金反应的动力学条件。熔池搅拌可藉助于气体、机械、电磁感应等方法来实现。
五、脱磷
减少钢液中含磷量的化学反应。磷是钢中有害杂质之一。含磷较多的钢,在室温或更低的温度下使用时,容易脆裂,称为"冷脆"。钢中含碳越高,磷引起的脆性越严重。一般普通钢中规定含磷量不超过 0.045%,优质钢要求含磷更少。生铁中的磷,主要来自铁矿石中的磷酸盐。氧化磷和氧化铁的热力学稳定性相近。在高炉的还原条件下,炉料中的磷几乎全部被还原并溶入铁水。如选矿不能除去磷的化合物,脱磷就只能在(高)炉外或碱性炼钢炉中进行。
铁中脱磷问题的认识和解决,在钢铁生产发展史上具有特殊的重要意义。钢的大规模工业生产开始于1856年贝塞麦(H.Bessemer)发明的酸性转炉炼钢法。但酸性转炉炼钢不能脱磷;而含磷低的铁矿石又很少,严重地阻碍了钢生产的发展。1879年托马斯(S.Thomas)发明了能处理高磷铁水的碱性转炉炼钢法,碱性炉渣的脱磷原理接着被推广到平炉炼钢中去,使大量含磷铁矿石得以用于生产钢铁,对现代钢铁工业的发展作出了重大的贡献
六、电炉底吹
电炉底吹:通过置于炉底的喷嘴将N2、Ar、CO2、CO、CH4、O2等气体根据工艺要求吹入炉内熔池以达到加速熔化,促进冶金反应过程的目的。采用底吹工艺可缩短冶炼时间,降低电耗,改善脱磷、脱硫操作,提高钢中残锰量,提高金属和合金收得率。并能使钢水成分、温度更均匀,从而改善钢质量,降低成本,提高生产率。
七、熔化期
熔化期:炼钢的熔化期主要是对平炉和电炉炼钢而言。电弧炉炼钢从通电开始到炉钢花伴料全部熔清为止、平炉炼钢从兑完铁水到炉料全部化完为止都称熔化期。熔化期的任务是尽快将炉料熔化及升温,并造好熔化期的炉渣。
八、氧化期
氧化期和脱碳期:普通功率电弧炉炼钢的氧化期,通常指炉料溶清、取样分析到扒完氧化渣这一工艺阶段。也有认为是从吹氧或加矿脱碳开始的。氧化期的主要任务是氧化钢液中的碳、磷;去除气体及夹杂物;使钢液均匀加热升温。脱碳是氧化期的一项重要操作工艺。为了保证钢的纯净度,要求脱碳量大于0.2%左右。随着炉外精炼技术的发展,电弧炉的氧化精炼大多移到钢包或精炼炉中进行。
九、精炼期
精炼期:炼钢过程通过造渣和其他方法把对钢的质量有害的一些元素和化合物,经化学反应选入气相或排、浮入渣中,使之从钢液中排除的工艺操作期。连铸机出坯
连铸机出坯
十、还原期
还原期:普通功率电弧炉炼钢操作中,通常把氧化末期扒渣完毕到出钢这段时间称为还原期。其主要任务是造还原渣进行扩散、脱氧、脱硫、控制化学成分和调整温度。高功率和超功率电弧炉炼钢操作已取消还原期。
十一、炉外精炼
炉外精炼:将炼钢炉(转炉、电炉等)中初炼过的钢液移到另一个容器中进行精炼的炼钢过程,也叫二次冶金。炼钢过程因此分为初炼和精炼两步进行。初炼:炉料在氧化性气氛的炉内进行熔化、脱磷、脱碳和主合金化。精炼:将初炼的钢液在真空、惰性气体或还原性气氛的容器中进行脱气、脱氧、脱硫,去除夹杂物和进行成分微调等。将炼钢分两步进行的好处是:可提高钢的质量,炼钢车间缩短冶炼时间,简化工艺过程并降低生产成本。炉外精炼的种类很多,大致可分为常压下炉外精炼和真空下炉外精炼两类。按处理方式的不同,又可分为钢包处理型炉外精炼及钢包精炼型炉外精炼等。
十二、钢液搅拌
钢液搅拌:炉外精炼过程中对钢液进行的搅拌。它使钢液成分和温度均匀化,并能促进冶金反应。多数冶金反应过程是相界面反应,反应物和生成物的扩散速度是这些反应的限制性环节。钢液在静止状态下,其冶金反应速度很慢,如电炉中静止的钢液脱硫需30~60分钟;而在炉精炼中采取搅拌钢液的办法脱硫只需3~5分钟。钢液在静止状态下,夹杂物上浮除去,排除速度较慢;搅拌钢液时,夹杂物的除去速度按指数规律递增,并与搅拌强度、类型和夹杂物的特性、浓度有关。
十三、钢包喂丝
钢包喂丝:通过喂丝机向钢包内喂入用铁皮包裹的脱氧、脱硫及微调成分的粉剂,如Ca-Si粉、或直接喂入铝线、碳线等对钢水进行深脱硫、钙处理以及微调钢中碳和铝等成分的方法。它还具有清洁钢水、改善非金属夹杂物形态的功能。
已赞过
已踩过<
评论
收起
你对这个回答的评价是?
2013-07-25
展开全部
粉末冶金工艺过程
粉末冶金材料是指不经熔炼和铸造,直接用几种金属粉末或金属粉末与非金属粉末,通过配制、压制成型,烧结和后处理等制成的材料。粉末冶金是金属冶金工艺与陶瓷烧结工艺的结合,它通常要经过以下几个工艺过程:
一、粉料制备与压制成型
常用机械粉碎、雾化、物理化学法制取粉末。制取的粉末经过筛分与混合,混料均匀并加入适当的增塑剂,再进行压制成型,粉粒间的原子通过固相扩散和机械咬合作用,使制件结合为具有一定强度的整体。压力越大则制件密度越大,强度相应增加。有时为减小压力合增加制件密度,也可采用热等静压成型的方法。
二、烧结
将压制成型的制件放置在采用还原性气氛的闭式炉中进行烧结,烧结温度约为基体金属熔点的2/3~3/4倍。由于高温下不同种类原子的扩散,粉末表面氧化物的被还原以及变形粉末的再结晶,使粉末颗粒相互结合,提高了粉末冶金制品的强度,并获得与一般合金相似的组织。经烧结后的制件中,仍然存在一些微小的孔隙,属于多孔性材料。
三、后处理
一般情况下,烧结好的制件能够达到所需性能,可直接使用。但有时还需进行必要的后处理。如精压处理,可提高制件的密度和尺寸形状精度;对铁基粉末冶金制件进行淬火、表面淬火等处理可改善其机械性能;为达到润滑或耐蚀目的而进行浸油或浸渍其它液态润滑剂;将低熔点金属渗入制件孔隙中去的熔渗处理,可提高制件的强度、硬度、可塑性或冲击韧性等。
粉末冶金工艺的优点
1、绝大多数难熔金属及其化合物、假合金、多孔材料只能用粉末冶金方法来制造。2、由于粉末冶金方法能压制成最终尺寸的压坯,而不需要或很少需要随后的机械加工,故能大大节约金属,降低产品成本。用粉末冶金方法制造产品时,金属的损耗只有1-5%,而用一般熔铸方法生产时,金属的损耗可能会达到80%。3、由于粉末冶金工艺在材料生产过程中并不熔化材料,也就不怕混入由坩埚和脱氧剂等带来的杂质,而烧结一般在真空和还原气氛中进行,不怕氧化,也不会给材料任何污染,故有可能制取高纯度的材料。
4、粉末冶金法能保证材料成分配比的正确性和均匀性。 5、粉末冶金适宜于生产同一形状而数量多的产品,特别是齿轮等加工费用高的产品,用粉末冶金法制造能大大降低生产成.(林里粉末)
粉末冶金是制取金属粉末,及采用成形和烧结工艺将金属粉末(或金属粉末与非金属粉末的混合物)制成材料和制品的工艺技术。它是冶金和材料科学的一个分支学科。
粉末冶金制品的应用范围十分广泛,从普通机械制造到精密仪器;从五金工具到大型机械;从电子工业到电机制造;从民用工业到军事工业;从一般技术到尖端高技术,均能见到粉末冶金工艺的身影。
粉末冶金材料是指不经熔炼和铸造,直接用几种金属粉末或金属粉末与非金属粉末,通过配制、压制成型,烧结和后处理等制成的材料。粉末冶金是金属冶金工艺与陶瓷烧结工艺的结合,它通常要经过以下几个工艺过程:
一、粉料制备与压制成型
常用机械粉碎、雾化、物理化学法制取粉末。制取的粉末经过筛分与混合,混料均匀并加入适当的增塑剂,再进行压制成型,粉粒间的原子通过固相扩散和机械咬合作用,使制件结合为具有一定强度的整体。压力越大则制件密度越大,强度相应增加。有时为减小压力合增加制件密度,也可采用热等静压成型的方法。
二、烧结
将压制成型的制件放置在采用还原性气氛的闭式炉中进行烧结,烧结温度约为基体金属熔点的2/3~3/4倍。由于高温下不同种类原子的扩散,粉末表面氧化物的被还原以及变形粉末的再结晶,使粉末颗粒相互结合,提高了粉末冶金制品的强度,并获得与一般合金相似的组织。经烧结后的制件中,仍然存在一些微小的孔隙,属于多孔性材料。
三、后处理
一般情况下,烧结好的制件能够达到所需性能,可直接使用。但有时还需进行必要的后处理。如精压处理,可提高制件的密度和尺寸形状精度;对铁基粉末冶金制件进行淬火、表面淬火等处理可改善其机械性能;为达到润滑或耐蚀目的而进行浸油或浸渍其它液态润滑剂;将低熔点金属渗入制件孔隙中去的熔渗处理,可提高制件的强度、硬度、可塑性或冲击韧性等。
粉末冶金工艺的优点
1、绝大多数难熔金属及其化合物、假合金、多孔材料只能用粉末冶金方法来制造。2、由于粉末冶金方法能压制成最终尺寸的压坯,而不需要或很少需要随后的机械加工,故能大大节约金属,降低产品成本。用粉末冶金方法制造产品时,金属的损耗只有1-5%,而用一般熔铸方法生产时,金属的损耗可能会达到80%。3、由于粉末冶金工艺在材料生产过程中并不熔化材料,也就不怕混入由坩埚和脱氧剂等带来的杂质,而烧结一般在真空和还原气氛中进行,不怕氧化,也不会给材料任何污染,故有可能制取高纯度的材料。
4、粉末冶金法能保证材料成分配比的正确性和均匀性。 5、粉末冶金适宜于生产同一形状而数量多的产品,特别是齿轮等加工费用高的产品,用粉末冶金法制造能大大降低生产成.(林里粉末)
粉末冶金是制取金属粉末,及采用成形和烧结工艺将金属粉末(或金属粉末与非金属粉末的混合物)制成材料和制品的工艺技术。它是冶金和材料科学的一个分支学科。
粉末冶金制品的应用范围十分广泛,从普通机械制造到精密仪器;从五金工具到大型机械;从电子工业到电机制造;从民用工业到军事工业;从一般技术到尖端高技术,均能见到粉末冶金工艺的身影。
已赞过
已踩过<
评论
收起
你对这个回答的评价是?
2013-07-25
展开全部
采矿(获得铁矿石)----选矿(将铁矿石破碎、磁选成铁精粉)---烧结(将铁精粉烧结成具有一定强度、粒度的烧结矿)---冶炼(将烧结矿运送至高炉,热风、焦碳使烧结矿还原成铁水,并脱硫)---炼钢(在转炉内高压氧气将铁水脱磷、去除夹杂,变成钢水)---精练(进一步脱磷、去除夹杂,提高纯净度)---连铸(热状态下将钢水铸成具有一定形状的连铸坯)---轧钢(将连铸坯轧制成用户要求的各种型号的钢材,如板材、线材、管材等)。
已赞过
已踩过<
评论
收起
你对这个回答的评价是?
展开全部
现代炼钢工艺主要的流程有那些?
钢与生铁的区别,首先是碳的含量,理论上一般把碳含量小于2.11%称之钢,它的熔点在1450-1500℃,生铁的含碳量在2.5-4.3%左右,而生铁的熔点在1100-1200℃。在钢中碳元素和铁元素形成Fe3C固熔体,随着碳含量的增加,其强度、硬度增加,而塑性和冲击韧性降低。南京麒麟仪器集团的检测设备可以精准的区分钢材原材料中的碳元素含量。
钢具有很好的物理、化学性能与力学性能,可进行拉、压、轧、冲、拔等深加工,其用途十分广泛。用途不同对钢的性能要求也不同,从而对钢的生产也提出了不同的要求。石油、化工、航天航空、交通运输、农业、国防等许多重要的领域均需要各种类型的大量钢材,我们的日常生活更离不开钢。总之,钢材仍将是21世纪用途最广的结构材料和最主要功能材料。
现代炼钢工艺主要的流程有两种
(长流程和短流程)
炼钢,目前主要有两条工艺路线,即转炉炼钢流程和电弧炉炼钢流程,通常 将“高炉-铁水预处理-转炉-精炼-连铸”称为长流程,而将“废钢-电弧炉-精炼连铸”称为短流程,短流程无需庞杂的铁前系统和高炉炼铁,因而,工艺简单、 投资低、建设周期短。但短流程生产规模相对较小,生产品种范围相对较窄,生产成本相对较高。同时受废钢和直接还原铁供应的限制,目前,大多数短流程钢 铁生产企业也开始建高炉和相应的铁前系统,电弧炉采用废钢+铁水热装技术吹氧熔炼钢水,可降低电耗,缩短冶炼周期,提高钢水品质。
1
长流程工艺
以氧气转炉炼钢工艺为中心的钢铁联合企业生产流程。高炉经还原冶炼得到的铁水,经铁水预处理兑入顶底复吹氧气转炉,经吹炼去除杂质,将钢水倒入钢包中,经二次精炼(如 RH、LF、VD 等)使钢水纯净化,然后钢水经凝固成型连铸成为钢坯,在经轧制工序最后成为钢材。
2
短流程工艺
以电炉炼钢工艺为中心的小钢厂生产流程。将回收再利用的废钢经破碎、分选加工后,经预热加入到电弧炉中,电弧炉利用电能做能源熔化废钢,去除杂质(如磷、硫)后出钢,再经二次精炼获得合格钢水,然后钢水经凝固成型连铸成为钢坯,在经轧制工序最后成为钢材。
钢与生铁的区别,首先是碳的含量,理论上一般把碳含量小于2.11%称之钢,它的熔点在1450-1500℃,生铁的含碳量在2.5-4.3%左右,而生铁的熔点在1100-1200℃。在钢中碳元素和铁元素形成Fe3C固熔体,随着碳含量的增加,其强度、硬度增加,而塑性和冲击韧性降低。南京麒麟仪器集团的检测设备可以精准的区分钢材原材料中的碳元素含量。
钢具有很好的物理、化学性能与力学性能,可进行拉、压、轧、冲、拔等深加工,其用途十分广泛。用途不同对钢的性能要求也不同,从而对钢的生产也提出了不同的要求。石油、化工、航天航空、交通运输、农业、国防等许多重要的领域均需要各种类型的大量钢材,我们的日常生活更离不开钢。总之,钢材仍将是21世纪用途最广的结构材料和最主要功能材料。
现代炼钢工艺主要的流程有两种
(长流程和短流程)
炼钢,目前主要有两条工艺路线,即转炉炼钢流程和电弧炉炼钢流程,通常 将“高炉-铁水预处理-转炉-精炼-连铸”称为长流程,而将“废钢-电弧炉-精炼连铸”称为短流程,短流程无需庞杂的铁前系统和高炉炼铁,因而,工艺简单、 投资低、建设周期短。但短流程生产规模相对较小,生产品种范围相对较窄,生产成本相对较高。同时受废钢和直接还原铁供应的限制,目前,大多数短流程钢 铁生产企业也开始建高炉和相应的铁前系统,电弧炉采用废钢+铁水热装技术吹氧熔炼钢水,可降低电耗,缩短冶炼周期,提高钢水品质。
1
长流程工艺
以氧气转炉炼钢工艺为中心的钢铁联合企业生产流程。高炉经还原冶炼得到的铁水,经铁水预处理兑入顶底复吹氧气转炉,经吹炼去除杂质,将钢水倒入钢包中,经二次精炼(如 RH、LF、VD 等)使钢水纯净化,然后钢水经凝固成型连铸成为钢坯,在经轧制工序最后成为钢材。
2
短流程工艺
以电炉炼钢工艺为中心的小钢厂生产流程。将回收再利用的废钢经破碎、分选加工后,经预热加入到电弧炉中,电弧炉利用电能做能源熔化废钢,去除杂质(如磷、硫)后出钢,再经二次精炼获得合格钢水,然后钢水经凝固成型连铸成为钢坯,在经轧制工序最后成为钢材。
已赞过
已踩过<
评论
收起
你对这个回答的评价是?
推荐律师服务:
若未解决您的问题,请您详细描述您的问题,通过百度律临进行免费专业咨询
广告 您可能关注的内容 |