
【精益管理】为什么企业需要变革?
1个回答
2023-01-31 · 为企业提供精益管理、运营管理的培训机构
关注
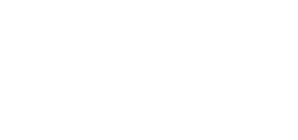
展开全部
随着社会分工越来越细和专业化程度越来越高,实施精益管理已经成为企业做大、做强的根本途径。精益管理是以细化管理为中心,要求对公司每一项经济业务,建立起一套细致入微的科学方法,并运用有效的手段进行合理管控,将管理的触角延伸到公司的方方面面和各个业务领域,助力企业挖掘各方面的潜力,从而实现公司利益最大化。
精益化管理是精益化生产最易于成效的手段,通过实施精益化生产管理,不仅可以大大改善员工的工作环境,而且可以大幅度提高生产效率,降低生产成本,提高产品质量,从而提高产品的市场竞争能力。
一、推进“精益管理”的鲜明目的和现实意义:
“精益管理”是一种先进的管理理念,其本质是利用最小的资源创造最大的价值,达到效益最大化。当今时代,作为服务类企业和服务类企业中的优秀企业,都应该进入到企业“精益管理”的阶段因为, 全面推进精益管理是强化企业管理工作的重要部署,是建设具有国际竞争力的一流企业的现实需要,是企业推进管理创新,向管理要效益、向管理要方法、向管理要进步的重要举措,对转变企业发展方式,提高企业发展质量和效益具有非常重要的意义。
二、精益管理的基本原则
1. 价值观:精益思想认为产品的价值应该由最终用户来决定,只有满足用户的特定需求,产品的价值才能存在。
2. 价值流:指从原材料到成品的所有活动。确定价值流是精益生产的出发点,并根据最终用户的位置寻求整个过程的整体最佳状态。
3.流动:精益生产强调各种价值创造活动需要流动,流动强调运动。
4. 拉动:拉动生产是指根据用户的需求拉动生产,而不是强行将产品推给用户。
5. 完美:完美价值是通过完美价值的创造过程提供给用户的。
三、推行精益化管理的措施及步骤
1、选择要改进的关键岗位
精益方式不是一蹴而就的,它强调的是持续改进。刚开始我们不宜全方位全公司铺开,首先应该选择某一生产线、车间、岗位或某一关键工艺流程作为试点,力争通过努力把它建立成一条样板车间或样板生产线,树立标杆,便于今后其他岗位或车间进行学习和推广。
2、设立目标管理看板
即绘制目前状态的看板,再描绘出一个精益远景图目标看板(可以选择一些典型企业的精益化管理的成功图示),同时配置以相应的奖励机制。树立起标杆和目标,给员工设定出美好的期望和梦想。
3、成立精益管理推进小组
可以将不同岗位甚至不同部门人员组合在一起,以此来推动精益化进程。只要有兴趣于创新和改革的人,都可以纳入进来,而这也是必须的一种精神,只有有兴趣才可能做的更好。
4、进行要因分析,找出需要改进的地方
以6S为基础,以改善环境和改进流程为突破口,以消除生产作业的八大浪费为重点,针对岗位的现状进行分析,找出需要改进和改良的地方或流程。
5、制定推进措施
在这个过程中,也可以做成看板,可以用更多的图标用来表示连续的流程和推进的进度,用各种类型的推进或改善图示,使目标更明确,并细化作业内容,如均衡生产、拉动系统(即以后道工序来自动拉动前道工序,缩短待工时间),甚至细化到生产周期(可以细分为增值时间和非增值时间),以此来消除不必要的时间浪费。
6、进行持续改进
精益远景图必须付诸实施,否则规划得再巧妙的图表也只是废纸一张。实施计划中包括什么,什么时间,谁来负责,并且在实施过程中设立评审节点。发放验收合格证或绿色通行证,才可以进入下一改善环节。这样,员工就自觉参与到整体了生产精益化管理的系统维护中。在目标看板、精益远景图的引导下,在小组成员推动下,在得力措施保证下,各个改善的项目被赋予了新的意义,使员工十分明确实施该项目的意义。持续改进生产流程的方法主要有以下几种:消除质量检测环节和返工现象;消除产品不必要的移动;消灭库存;合理安排生产计划;减少生产准备时间;消除停机待工时间;提高劳动利用率。
7、推广到整个公司
精益生产管理最后是要在生产上消除浪费,着眼于整个生产流程,而不只是个别岗位或某个工序。所以,关键岗位的样板成功经验要推广到整个生产管理,甚至于全公司,使操作工序更简单,工作效率更高,成本费用更低,最后达到整个公司的精益化管理目标得以实现。
8、营造企业文化
经过推行精益化生产管理,必将在车间现场发生的显著改进,并能引发随后一系列企业文化变革。文化的变革要比生产现场的改进难度更大,两者都是必须完成并且是相辅相成的。传统管理向精益化生产管理转变,必然使推行精益化管理的员工的思想和理念都发生了翻天覆地的变化,我们可以借助这一改变,逐步去营造适合自己的企业文化。
精益化管理就是将管理延伸到横向到边,纵向到底,从细微处着眼,从一点一滴抓起,从浪费抓起,从节约抓起,环环相扣,丝丝相连,用优良的方法来促进管理,用科学的手段来推动经营。通过精益化管理可以推动整个经营的革新,推动整个团队的改善,推动员工干事创业的积极性主动性,进而推动企业业绩目标的实现。
精益化管理是精益化生产最易于成效的手段,通过实施精益化生产管理,不仅可以大大改善员工的工作环境,而且可以大幅度提高生产效率,降低生产成本,提高产品质量,从而提高产品的市场竞争能力。
一、推进“精益管理”的鲜明目的和现实意义:
“精益管理”是一种先进的管理理念,其本质是利用最小的资源创造最大的价值,达到效益最大化。当今时代,作为服务类企业和服务类企业中的优秀企业,都应该进入到企业“精益管理”的阶段因为, 全面推进精益管理是强化企业管理工作的重要部署,是建设具有国际竞争力的一流企业的现实需要,是企业推进管理创新,向管理要效益、向管理要方法、向管理要进步的重要举措,对转变企业发展方式,提高企业发展质量和效益具有非常重要的意义。
二、精益管理的基本原则
1. 价值观:精益思想认为产品的价值应该由最终用户来决定,只有满足用户的特定需求,产品的价值才能存在。
2. 价值流:指从原材料到成品的所有活动。确定价值流是精益生产的出发点,并根据最终用户的位置寻求整个过程的整体最佳状态。
3.流动:精益生产强调各种价值创造活动需要流动,流动强调运动。
4. 拉动:拉动生产是指根据用户的需求拉动生产,而不是强行将产品推给用户。
5. 完美:完美价值是通过完美价值的创造过程提供给用户的。
三、推行精益化管理的措施及步骤
1、选择要改进的关键岗位
精益方式不是一蹴而就的,它强调的是持续改进。刚开始我们不宜全方位全公司铺开,首先应该选择某一生产线、车间、岗位或某一关键工艺流程作为试点,力争通过努力把它建立成一条样板车间或样板生产线,树立标杆,便于今后其他岗位或车间进行学习和推广。
2、设立目标管理看板
即绘制目前状态的看板,再描绘出一个精益远景图目标看板(可以选择一些典型企业的精益化管理的成功图示),同时配置以相应的奖励机制。树立起标杆和目标,给员工设定出美好的期望和梦想。
3、成立精益管理推进小组
可以将不同岗位甚至不同部门人员组合在一起,以此来推动精益化进程。只要有兴趣于创新和改革的人,都可以纳入进来,而这也是必须的一种精神,只有有兴趣才可能做的更好。
4、进行要因分析,找出需要改进的地方
以6S为基础,以改善环境和改进流程为突破口,以消除生产作业的八大浪费为重点,针对岗位的现状进行分析,找出需要改进和改良的地方或流程。
5、制定推进措施
在这个过程中,也可以做成看板,可以用更多的图标用来表示连续的流程和推进的进度,用各种类型的推进或改善图示,使目标更明确,并细化作业内容,如均衡生产、拉动系统(即以后道工序来自动拉动前道工序,缩短待工时间),甚至细化到生产周期(可以细分为增值时间和非增值时间),以此来消除不必要的时间浪费。
6、进行持续改进
精益远景图必须付诸实施,否则规划得再巧妙的图表也只是废纸一张。实施计划中包括什么,什么时间,谁来负责,并且在实施过程中设立评审节点。发放验收合格证或绿色通行证,才可以进入下一改善环节。这样,员工就自觉参与到整体了生产精益化管理的系统维护中。在目标看板、精益远景图的引导下,在小组成员推动下,在得力措施保证下,各个改善的项目被赋予了新的意义,使员工十分明确实施该项目的意义。持续改进生产流程的方法主要有以下几种:消除质量检测环节和返工现象;消除产品不必要的移动;消灭库存;合理安排生产计划;减少生产准备时间;消除停机待工时间;提高劳动利用率。
7、推广到整个公司
精益生产管理最后是要在生产上消除浪费,着眼于整个生产流程,而不只是个别岗位或某个工序。所以,关键岗位的样板成功经验要推广到整个生产管理,甚至于全公司,使操作工序更简单,工作效率更高,成本费用更低,最后达到整个公司的精益化管理目标得以实现。
8、营造企业文化
经过推行精益化生产管理,必将在车间现场发生的显著改进,并能引发随后一系列企业文化变革。文化的变革要比生产现场的改进难度更大,两者都是必须完成并且是相辅相成的。传统管理向精益化生产管理转变,必然使推行精益化管理的员工的思想和理念都发生了翻天覆地的变化,我们可以借助这一改变,逐步去营造适合自己的企业文化。
精益化管理就是将管理延伸到横向到边,纵向到底,从细微处着眼,从一点一滴抓起,从浪费抓起,从节约抓起,环环相扣,丝丝相连,用优良的方法来促进管理,用科学的手段来推动经营。通过精益化管理可以推动整个经营的革新,推动整个团队的改善,推动员工干事创业的积极性主动性,进而推动企业业绩目标的实现。
推荐律师服务:
若未解决您的问题,请您详细描述您的问题,通过百度律临进行免费专业咨询