
正火,回火,退火,淬火的区别是什么?
正火,回火,退火,淬火的区别在于工艺不同、材料组织变化不同、材料性能改变结果不同。
1、工艺不同:
正火是将工件加热至Ac3(Ac是指加热时自由铁素体全部转变为奥氏体的终了温度,一般是从727℃到912℃之间)或Acm(Acm是实际加热中过共析钢完全奥氏体化的临界温度线 )以上30~50℃,保温一段时间后,从炉中取出在空气中或喷水、喷雾或吹风冷却的金属热处理工艺。
回火处理是指将经过淬火硬化或正常化处理之钢材在浸置于一低于临界温度一段时间后,以一定的速率冷却下来。
退火是将金属加热到一定温度,保持足够时间,然后以适宜速度冷却(通常是缓慢冷却,有时是控制冷却)的一种金属热处理工艺。
钢的淬火是将钢加热到临界温度Ac3(亚共析钢)或Ac1(过共析钢)以上温度,保温一段时间,使之全部或部分奥氏体化,然后以大于临界冷却速度的冷速快冷到Ms以下(或Ms附近等温)进行马氏体(或贝氏体)转变的热处理工艺。
2、材料组织变化不同:
正火后的组织:亚共析钢为铁素体+珠光体,共析钢为珠光体,过共析钢为珠光体+二次渗碳体,且为不连续。
低温回火得到的是马氏体组织;中温回火得到的组织为回火托氏体;高温回火调质处理得到的是回火索氏体组织。
退火后细化晶粒,调整组织,消除组织缺陷。
淬火使过冷奥氏体进行马氏体或贝氏体转变,得到马氏体或贝氏体组织,最后获得以马氏体为主的不平衡组织(也有根据需要获得贝氏体或保持单相奥氏体)。
3、材料性能改变结果不同:
正火时可在稍快的冷却中使钢材的结晶晶粒细化,不但可得到满意的强度,而且可以明显提高韧性(AKV值),降低构件的开裂倾向。—些低合金热轧钢板、低合金钢锻件与铸造件经正火处理后,材料的综合力学性能可以大大改善,而且也改善了切削性能。
回火后将经过淬火及正常化处理在放回中温浸置(时效)一段时间,可促使一部分之碳化物析出,同时有可消除一部分因急速冷却所造成之残留应力,因此可提高材料之韧性与柔性。
退火能够降低硬度,改善切削加工性.消除残余应力,稳定尺寸,减少变形与裂纹倾向;细化晶粒,调整组织,消除组织缺陷。均匀材料组织和成分,改善材料性能或为以后热处理做组织准备。
淬火能大幅提高钢的刚性、硬度、耐磨性、疲劳强度以及韧性等,从而满足各种机械零件和工具的不同使用要求。也可以通过淬火满足某些特种钢材的铁磁性、耐蚀性等特殊的物理、化学性能。
参考资料:百度百科-正火
参考资料:百度百科-回火处理
参考资料:百度百科-退火处理
参考资料:百度百科-淬火
推荐于2017-12-18
把钢加热到一定温度并在此温度下保温,然后缓慢冷却到室温.
退火有完全退火、球化退火、去应力退火等几种。
a将钢加热到预定温度,保温一段时间,然后随炉缓慢冷却称为完全退火.目的是降低钢的硬度,消除钢中不均匀组织和内应力.
b,把钢加热到750度,保温一段时间,缓慢冷却至500度下,最后在空气中冷却叫球化退火.目的是降低钢的硬度,改善切削性能,主要用于高碳钢.
c,去应力退火又叫低温退火,把钢加热到500~600度,保温一段时间,随炉缓冷到300度以下,再室温冷却.退火过程中组织不发生变化,主要消除金属的内应力.
2.正火
将钢件加热到临界温度以上30-50℃,保温适当时间后,在静止的空气中冷却的热处理工艺称为正火。
正火的主要目的是细化组织,改善钢的性能,获得接近平衡状态的组织。
正火与退火工艺相比,其主要区别是正火的冷却速度稍快,所以正火热处理的生产周期短。故退火与正火同样能达到零件性能要求时,尽可能选用正火。
3.淬火
将钢件加热到临界点以上某一温度(45号钢淬火温度为840-860℃,碳素工具钢的淬火温度为760~780℃),保持一定的时间,然后以适当速度在水(油)中冷却以获得马氏体或贝氏体组织的热处理工艺称为淬火。
淬火与退火、正火处理在工艺上的主要区别是冷却速度快,目的是为了获得马氏体组织。马氏体组织是钢经淬火后获得的不平衡组织,它的硬度高,但塑性、韧性差。马氏体的硬度随钢的含碳量提高而增高。
4.回火
钢件淬硬后,再加热到临界温度以下的某一温度,保温一定时间,然后冷却到室温的热处理工艺称为回火。
淬火后的钢件一般不能直接使用,必须进行回火后才能使用。因为淬火钢的硬度高、脆性大,直接使用常发生脆断。通过回火可以消除或减少内应力、降低脆性,提高韧性;另一方面可以调整淬火钢的力学性能,达到钢的使用性能。根据回火温度的不同,回火可分为低温回火、中温回火和高温回火三种。
A 低温回火150~250.降低内应力,脆性,保持淬火后的高硬度和耐磨性.
B 中温回火350~500;提高弹性,强度.
C 高温回火500~650;淬火钢件在高于500℃的回火称为高温回火。淬火钢件经高温淬火后,具有良好综合力学性能(既有一定的强度、硬度,又有一定的塑性、韧性)。所以一般中碳钢和中碳合金钢常采用淬火后的高温回火处理。轴类零件应用最多。
淬火+高温回火称为调质处理。
2021-09-29 · 百度认证:深圳市瀚辉石墨有限公司官方账号
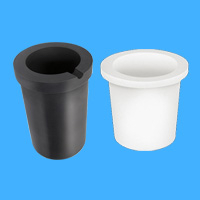
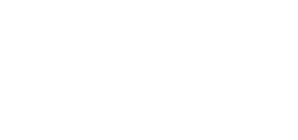
把钢加热到一定温度并在此温度下保温,然后缓慢冷却到室温.
退火有完全退火、球化退火、去应力退火等几种。
a将钢加热到预定温度,保温一段时间,然后随炉缓慢冷却称为完全退火.目的是降低钢的硬度,消除钢中不均匀组织和内应力.
b,把钢加热到750度,保温一段时间,缓慢冷却至500度下,最后在空气中冷却叫球化退火.目的是降低钢的硬度,改善切削性能,主要用于高碳钢.
c,去应力退火又叫低温退火,把钢加热到500~600度,保温一段时间,随炉缓冷到300度以下,再室温冷却.退火过程中组织不发生变化,主要消除金属的内应力.
2.正火
将钢件加热到临界温度以上30-50℃,保温适当时间后,在静止的空气中冷却的热处理工艺称为正火。
正火的主要目的是细化组织,改善钢的性能,获得接近平衡状态的组织。
正火与退火工艺相比,其主要区别是正火的冷却速度稍快,所以正火热处理的生产周期短。故退火与正火同样能达到零件性能要求时,尽可能选用正火。
3.淬火
将钢件加热到临界点以上某一温度(45号钢淬火温度为840-860℃,碳素工具钢的淬火温度为760~780℃),保持一定的时间,然后以适当速度在水(油)中冷却以获得马氏体或贝氏体组织的热处理工艺称为淬火。
淬火与退火、正火处理在工艺上的主要区别是冷却速度快,目的是为了获得马氏体组织。马氏体组织是钢经淬火后获得的不平衡组织,它的硬度高,但塑性、韧性差。马氏体的硬度随钢的含碳量提高而增高。
4.回火
钢件淬硬后,再加热到临界温度以下的某一温度,保温一定时间,然后冷却到室温的热处理工艺称为回火。
淬火后的钢件一般不能直接使用,必须进行回火后才能使用。因为淬火钢的硬度高、脆性大,直接使用常发生脆断。通过回火可以消除或减少内应力、降低脆性,提高韧性;另一方面可以调整淬火钢的力学性能,达到钢的使用性能。根据回火温度的不同,回火可分为低温回火、中温回火和高温回火三种。
A 低温回火150~250.降低内应力,脆性,保持淬火后的高硬度和耐磨性.
B 中温回火350~500;提高弹性,强度.
C 高温回火500~650;淬火钢件在高于500℃的回火称为高温回火。淬火钢件经高温淬火后,具有良好综合力学性能(既有一定的强度、硬度,又有一定的塑性、韧性)。所以一般中碳钢和中碳合金钢常采用淬火后的高温回火处理。轴类零件应用最多。
淬火+高温回火称为调质处理
淬火、回火、正火、退火之间,到底有何不同?今天算长见识了