
金属磨削工艺有哪些常见工艺问题?
1个回答
2019-06-11 · 工程机械属具,矿山机械设备、机床附件大全
关注
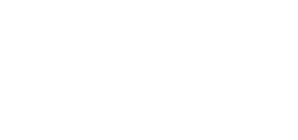
展开全部
金属磨削工艺是靠切削工件表面凸部而得到平滑面的工艺方法,磨削是机器零件精密制造的主要方法之一。对于精度要求高的及淬火零件,一般均采用磨削的方法。平磨时对于简单的铁磁性材料,可用电磁吸盘装夹工件;对于形状复杂或非铁磁性材料,可先用精密平口虎钳或专用夹具装夹,再用电磁吸盘或真空吸盘吸牢以保证工件的稳定。
一、磨床设备的常见类型
(1)卧轴矩台磨床
工件由矩形电磁操作台吸住或夹持并作纵向往复移动,砂磨架可沿滑座的燕尾导轨作横向间歇进给。滑座可沿立柱的导轨作垂直间歇进给,磨削工件磨削精度较高。
(2)立轴圆台磨床
竖直安置的砂磨主轴以砂轮端面磨削工件,砂轮架可沿立柱的导轨作间歇的垂直进给。工件装在旋转的圆操作台上可连续磨削。为了便于装卸工件,圆操作台还能沿床身导轨作纵向移动。
(3)卧轴圆台磨床
用于磨削圆形薄片工件,并可利用操作台倾斜磨出厚薄不等的环形工件。
(4)立轴矩台磨床
由于砂轮直径大于操作台宽度,磨削面积较大,适用于高效磨削。
二、磨削工艺的常见问题
(1)磨削工艺精度问题
磨削精度主要由机床精度、夹具精度和上述磨削工艺参数综合形成的。磨座面时的摆动区间的准确稳定将会影响座面母线的直线度,所以合理确定数控机床磨削参数。
(2)磨削工艺烧伤问题
磨削过程中工艺参数不合理或毛坯的尺寸精度控制不好会出现磨削烧伤的现象,这种磨削烧伤产生的主要因素有砂磨的线速度低、切削力低、砂磨和工件表面法向受力大等。
(3)磨削工艺裂纹问题
当磨削参数选择不合理,砂磨状态不好产生单点磨削时或者零件热处理后有残余应力存在时,磨削后中孔座面磨削表面会产生裂纹或细微裂纹,产生裂纹和细微裂纹特别在座面压力室处的裂纹将使座面前缘产生穴蚀,使工件的疲劳强度下降,一段时间后会早期失效。
(4)磨削工艺润滑问题
磨削油在磨削过程中主要起到润滑、冷却、清洗等作用,有时由于使用的磨削油性能不符合工艺要求,在高转速时无法深入到深孔表面,会产生氧化膜和硬化层使工件硬度不均匀,尤其是喷油嘴的座面磨削常会出现这种情况。导致工件的耐磨性、耐腐蚀性和疲劳强度大幅下降,缩短了油嘴的使用寿命。
三、磨削工艺的技术方案
(1)磨削工艺的装夹方式
磨削时以校正精度后的大外圆和工艺角,单薄膜夹头夹持大外圆,这样夹紧的方式可以避免中孔座面磨削轴向跳动。
(2)磨削工艺的切削余量
切削余量是保证高效高精度复合磨削的一个重要参数,通常精磨余量都控制在微米级别,考虑到装夹时的跳动等因素。
(3)磨削砂磨的选择方法
现代磨削技术都采用高速磨削,砂磨的选用,粘结剂的配比,砂磨的烧结气孔都要反复的试验,以保证砂磨在磨削的过程中保持良好的自锐性。
(4)磨削工件的旋转转速
工件转速和磨削表面的直径有关,工件的转速会对磨削切痕和表面粗糙度产生较大的影响,过低的转速会使磨削表面产生波纹,增大表面残余应力,转速过高会会引起磨削表面烧伤。
(5)磨削主轴的功率转速
磨削中砂磨的线速度是一个很重要的因素,现在磨削发展的方向是砂磨线速度不断提高。高速磨削主要有工件变形小、砂磨寿命长、质量高等优点。
(6)磨削主轴的进给速度
横向进给摆动速度和纵向切削速度应当配合试验、横向摆动速度过快,切削率要求高容易造成挤压砂磨,以保证磨削中孔的锥度。
四、磨削油品的选用方法
高速磨削油在轴承磨削制造工艺中起到了关键性的作用,良好的冷却性能和极压抗磨性能对于砂轮的使用寿命和轴承精度的提升有了质的飞跃。
(1)磨削油的极压性能
专用的磨削油含有硫化极压抗磨添加剂成分,可以有效的保护磨具,提高工艺精度。
(2)磨削油的化学性能
专用的磨削油与菜籽油、机械油、再生油相比,具有良好的化学稳定性,不会对设备、人体、环境产生危害。
(3)磨削油的其他性能
专用的磨削油在粘度、闪点、倾点、导热性能等方面均通过严格的测试,以满足各种工艺需求。
一、磨床设备的常见类型
(1)卧轴矩台磨床
工件由矩形电磁操作台吸住或夹持并作纵向往复移动,砂磨架可沿滑座的燕尾导轨作横向间歇进给。滑座可沿立柱的导轨作垂直间歇进给,磨削工件磨削精度较高。
(2)立轴圆台磨床
竖直安置的砂磨主轴以砂轮端面磨削工件,砂轮架可沿立柱的导轨作间歇的垂直进给。工件装在旋转的圆操作台上可连续磨削。为了便于装卸工件,圆操作台还能沿床身导轨作纵向移动。
(3)卧轴圆台磨床
用于磨削圆形薄片工件,并可利用操作台倾斜磨出厚薄不等的环形工件。
(4)立轴矩台磨床
由于砂轮直径大于操作台宽度,磨削面积较大,适用于高效磨削。
二、磨削工艺的常见问题
(1)磨削工艺精度问题
磨削精度主要由机床精度、夹具精度和上述磨削工艺参数综合形成的。磨座面时的摆动区间的准确稳定将会影响座面母线的直线度,所以合理确定数控机床磨削参数。
(2)磨削工艺烧伤问题
磨削过程中工艺参数不合理或毛坯的尺寸精度控制不好会出现磨削烧伤的现象,这种磨削烧伤产生的主要因素有砂磨的线速度低、切削力低、砂磨和工件表面法向受力大等。
(3)磨削工艺裂纹问题
当磨削参数选择不合理,砂磨状态不好产生单点磨削时或者零件热处理后有残余应力存在时,磨削后中孔座面磨削表面会产生裂纹或细微裂纹,产生裂纹和细微裂纹特别在座面压力室处的裂纹将使座面前缘产生穴蚀,使工件的疲劳强度下降,一段时间后会早期失效。
(4)磨削工艺润滑问题
磨削油在磨削过程中主要起到润滑、冷却、清洗等作用,有时由于使用的磨削油性能不符合工艺要求,在高转速时无法深入到深孔表面,会产生氧化膜和硬化层使工件硬度不均匀,尤其是喷油嘴的座面磨削常会出现这种情况。导致工件的耐磨性、耐腐蚀性和疲劳强度大幅下降,缩短了油嘴的使用寿命。
三、磨削工艺的技术方案
(1)磨削工艺的装夹方式
磨削时以校正精度后的大外圆和工艺角,单薄膜夹头夹持大外圆,这样夹紧的方式可以避免中孔座面磨削轴向跳动。
(2)磨削工艺的切削余量
切削余量是保证高效高精度复合磨削的一个重要参数,通常精磨余量都控制在微米级别,考虑到装夹时的跳动等因素。
(3)磨削砂磨的选择方法
现代磨削技术都采用高速磨削,砂磨的选用,粘结剂的配比,砂磨的烧结气孔都要反复的试验,以保证砂磨在磨削的过程中保持良好的自锐性。
(4)磨削工件的旋转转速
工件转速和磨削表面的直径有关,工件的转速会对磨削切痕和表面粗糙度产生较大的影响,过低的转速会使磨削表面产生波纹,增大表面残余应力,转速过高会会引起磨削表面烧伤。
(5)磨削主轴的功率转速
磨削中砂磨的线速度是一个很重要的因素,现在磨削发展的方向是砂磨线速度不断提高。高速磨削主要有工件变形小、砂磨寿命长、质量高等优点。
(6)磨削主轴的进给速度
横向进给摆动速度和纵向切削速度应当配合试验、横向摆动速度过快,切削率要求高容易造成挤压砂磨,以保证磨削中孔的锥度。
四、磨削油品的选用方法
高速磨削油在轴承磨削制造工艺中起到了关键性的作用,良好的冷却性能和极压抗磨性能对于砂轮的使用寿命和轴承精度的提升有了质的飞跃。
(1)磨削油的极压性能
专用的磨削油含有硫化极压抗磨添加剂成分,可以有效的保护磨具,提高工艺精度。
(2)磨削油的化学性能
专用的磨削油与菜籽油、机械油、再生油相比,具有良好的化学稳定性,不会对设备、人体、环境产生危害。
(3)磨削油的其他性能
专用的磨削油在粘度、闪点、倾点、导热性能等方面均通过严格的测试,以满足各种工艺需求。
推荐律师服务:
若未解决您的问题,请您详细描述您的问题,通过百度律临进行免费专业咨询