
焊接缺陷有哪些?
2个回答
2022-11-02 · 百度认证:北京惠企网络技术有限公司官方账号
关注
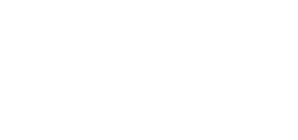
展开全部
常见的外观缺陷有咬边、焊瘤、凹陷及焊接变形等,有时还有表面气孔和表面裂纹。单面焊的根部未焊透等。
咬边是指沿着焊趾,在母材部分形成的凹陷或沟槽,它是由于电弧将焊缝边缘的母材熔化后没有得到熔敷金属的充分补充所留下的缺口。
产生咬边的主要原因是电弧热量太高,即电流太大,运条速度太小所造成的。
焊条与工件间角度不正确,摆动不合理,电弧过长,焊接次序不合理等都会造成咬边。直流焊时电弧的磁偏吹也是产生咬边的一个原因。某些焊接位置(立、横、仰)会加剧咬边。
咬边减小了母材的有效截面积,降低结构的承载能力,同时还会造成应力集中,发展为裂纹源。
矫正操作姿势,选用合理的规范,采用良好的运条方式都会有利于消除咬边。焊角焊缝时,用交流焊代替直流焊也能有效地防止咬边。
咬边是指沿着焊趾,在母材部分形成的凹陷或沟槽,它是由于电弧将焊缝边缘的母材熔化后没有得到熔敷金属的充分补充所留下的缺口。
产生咬边的主要原因是电弧热量太高,即电流太大,运条速度太小所造成的。
焊条与工件间角度不正确,摆动不合理,电弧过长,焊接次序不合理等都会造成咬边。直流焊时电弧的磁偏吹也是产生咬边的一个原因。某些焊接位置(立、横、仰)会加剧咬边。
咬边减小了母材的有效截面积,降低结构的承载能力,同时还会造成应力集中,发展为裂纹源。
矫正操作姿势,选用合理的规范,采用良好的运条方式都会有利于消除咬边。焊角焊缝时,用交流焊代替直流焊也能有效地防止咬边。
展开全部
常见的外观缺陷有咬边、焊瘤、凹陷及焊接变形等,有时还有表面气孔和表面裂纹。单面焊的根部未焊透等。
咬边:是指沿着焊趾,在母材部分形成的凹陷或沟槽, 它是由于电弧将焊缝边缘的母材熔化后没有得到熔敷金属的充分补充所留下的缺口。
焊瘤:焊缝中的液态金属流到加热不足未熔化的母材上或从焊缝根部溢出,冷却后形成的未与母材熔合的金属瘤即为焊瘤。焊接规范过强、焊条熔化过快、焊条质量欠佳(如偏芯),焊接电源特性不稳定及操作姿势不当等都容易带来焊瘤。
凹坑:指焊缝表面或背面局部的低于母材的部分。
未焊满:是指焊缝表面上连续的或断续的沟槽。填充金属不足是产生未焊满的根本原因。规范太弱,焊条过细,运条不当等会导致未焊满。
烧穿:是指焊接过程中,熔深超过工件厚度,熔化金属自焊缝背面流出,形成穿孔性缺。
其他表面缺陷:
(1)成形不良 指焊缝的外观几何尺寸不符合要求。有焊缝超高,表面不光滑,以及焊缝过宽,焊缝向母材过渡不圆滑等。
(2)错边指两个工件在厚度方向上错开一定位置,它既可视作焊缝表面缺陷,又可视作装配成形缺陷。
(3)塌陷 单面焊时由于输入热量过大,熔化金属过多而使液态金属向焊缝背面塌落, 成形后焊缝背面突起,正面下塌。
(4)表面气孔及弧坑缩孔。
(5)各种焊接变形如角变形、扭曲、波浪变形等都属于焊接缺陷O角变形也属于装配成形缺陷。
焊接接头的不完整性称为焊接缺欠,主要有焊接裂纹、未焊透、夹渣、气孔和焊缝外观缺欠等。这些缺欠减少焊缝截面积,降低承载能力,产生应力集中,引起裂纹;降低疲劳强度,易引起焊件破裂导致脆断。其中危害最大的是焊接裂纹和未熔合。
咬边:是指沿着焊趾,在母材部分形成的凹陷或沟槽, 它是由于电弧将焊缝边缘的母材熔化后没有得到熔敷金属的充分补充所留下的缺口。
焊瘤:焊缝中的液态金属流到加热不足未熔化的母材上或从焊缝根部溢出,冷却后形成的未与母材熔合的金属瘤即为焊瘤。焊接规范过强、焊条熔化过快、焊条质量欠佳(如偏芯),焊接电源特性不稳定及操作姿势不当等都容易带来焊瘤。
凹坑:指焊缝表面或背面局部的低于母材的部分。
未焊满:是指焊缝表面上连续的或断续的沟槽。填充金属不足是产生未焊满的根本原因。规范太弱,焊条过细,运条不当等会导致未焊满。
烧穿:是指焊接过程中,熔深超过工件厚度,熔化金属自焊缝背面流出,形成穿孔性缺。
其他表面缺陷:
(1)成形不良 指焊缝的外观几何尺寸不符合要求。有焊缝超高,表面不光滑,以及焊缝过宽,焊缝向母材过渡不圆滑等。
(2)错边指两个工件在厚度方向上错开一定位置,它既可视作焊缝表面缺陷,又可视作装配成形缺陷。
(3)塌陷 单面焊时由于输入热量过大,熔化金属过多而使液态金属向焊缝背面塌落, 成形后焊缝背面突起,正面下塌。
(4)表面气孔及弧坑缩孔。
(5)各种焊接变形如角变形、扭曲、波浪变形等都属于焊接缺陷O角变形也属于装配成形缺陷。
焊接接头的不完整性称为焊接缺欠,主要有焊接裂纹、未焊透、夹渣、气孔和焊缝外观缺欠等。这些缺欠减少焊缝截面积,降低承载能力,产生应力集中,引起裂纹;降低疲劳强度,易引起焊件破裂导致脆断。其中危害最大的是焊接裂纹和未熔合。
本回答被网友采纳
已赞过
已踩过<
评论
收起
你对这个回答的评价是?
推荐律师服务:
若未解决您的问题,请您详细描述您的问题,通过百度律临进行免费专业咨询