
为什么企业导入精益管理不成功呢
2016-03-14 · 最值得信赖的管理咨询专业机构
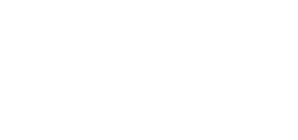
精益生产是中国公司导入的领先管理模式之一,虽有的公司导入精益生产成功了,但仍是有许多的公司在导入精益生产的活动中以失利告终,为何公司导入精益生产项目不成功呢?
谈到精益生产管理估计大家已不生疏,甚至有的会说:“咱们公司曾经也导入过精益生产管理,作用不怎么样啊”。状况确实是这样,从精益生产管理进入我国前期,大家如获至宝纷繁引入,却只有极少数的公司获得一些成效,绝大数公司没有获得想要的作用。这时呈现对精益生产管理大多是怀疑、否定的声响,从事精益生产咨询的公司,也被看着是骗子。为何一套被国外实践证明非常有效的管理系统,来到我国竟如此不服水土呢?
【失败的真正原因】:
关键在于多数实践者生搬硬套,没有结合公司实际情况,没有活用精益生产管理。对精益生产管理的认识停留在生产制造中运用一些工具办法等表层窍门,更有甚者,理解为硬件技术改造,投入很多资金,而公司职工思想方法和行为习惯没有一点点改变,所以导入精益生产管理不成功也是天经地义的。
精益生产管理的东西方法属技能层面常识,是套路,看多几遍就懂了。而每个企业实际情况、价值理念、行动特征都不一样,这就需求咱们捉住精益生产管理的根本,不要舍本求末。
【精益生产的核心认识】
要让精益生产管理在公司发挥出应有的作用,就有必要正确认识精益生产管理的中心思维。精益生产理念提倡的是以最大限度地减少企业所占用的资源和降低企业管理和营运成本为主要目标的生产方式,其以“消除浪费、持续改善”为理念,通过对生产方式进行不断的改进,消除原材料的浪费,进一步完善操作程序、提高产品的质量,进而缩短产品生产时间等持续减少企业运营中的非增值活动。精益生产和浪费(muda)直接对立。浪费包括很多类型,如闲置的库存、不必要的工序、不必要的工序、不必要的运输、超过需求的生产、人员的不必要动作、各种等待等,所有这些日常生产中很少为人们所注意但却大量存在。从企业获取订单到生产过程,再到最后的销售,消除浪费的思想贯穿始终。
精益生产管理源于制作,精益生产管理的最终目标是降低成本,怎么减少成本需要才智。不是偷工减料,也不是降低标准,以次充好;更不是减薪酬,降福利。而是在咱们作业中做了很多没有价值的作业,存在着很多糟蹋,避免了这些糟蹋,成本也就自然降低了。精益生产管理的作用好不好,就要看咱们消除浪费到底彻不彻底。
内容摘自:天行健咨询
企业精益生产可以按照如下步骤导入:
1、选择要改进的关键流程
精益生产方式不是一蹴而就的,它强调持续的改进。首先应该先选择关键的流程,力争把它建立成一条样板线。
2、画出价值流程图
价值流程图是一种用来描述物流和信息流的方法。在绘制完目前状态的价值流程图后,可以描绘出一个精益远景图(Future Lean Vision)。在这个过程中,更多的图标用来表示连续的流程,各种类型的拉动系统,均衡生产以及缩短工装更换时间,生产周期被细分为增值时间和非增值时间。
3、开展持续改进研讨会
精益远景图必须付诸实施,否则规划得再巧妙的图表也只是废纸一张。实施计划中包括什么(What),什么时候(When)和谁来负责(Who),并且在实施过程中设立评审节点。这样,全体员工都参与到全员生产性维护系统中。在价值流程图、精益远景图的指导下,流程上的各个独立的改善项目被赋予了新的意义,使员工十分明确实施该项目的意义。持续改进生产流程的方法主要有以下几种:消除质量检测环节和返工现象;消除零件不必要的移动;消灭库存;合理安排生产计划;减少生产准备时间;消除停机时间;提高劳动利用率。
4、营造企业文化
虽然在车间现场发生的显著改进,能引发随后一系列企业文化变革,但是如果想当然地认为由于车间平面布置和生产操作方式上的改进,就能自动建立和推进积极的文化改变,这显然是不现实的。文化的变革要比生产现场的改进难度更大,两者都是必须完成并且是相辅相成的。许多项目的实施经验证明,项目成功的关键是公司领导要身体力行地把生产方式的改善和企业文化的演变结合起来。
传统企业向精益化生产方向转变,不是单纯地采用相应的“看板”工具及先进的生产管理技术就可以完成,而必须使全体员工的理念发生改变。精益化生产之所以产生于日本,而不是诞生在美国,其原因也正因为两国的企业文化有相当大的不同。
5、推广到整个企业
精益生产利用各种工业工程技术来消除浪费,着眼于整个生产流程,而不只是个别或几个工序。所以,样板线的成功要推广到整个企业,使操作工序缩短,推动式生产系统被以顾客为导向的拉动式生产系统所替代。