
SMT识别贴片元件的方向和加工细则,有谁知道的?
展开全部
PCB上有些元件是有方向的,像贴片百二极管,
贴片机不会把二极管度方向搞错有标识。
不会自动贴错,除非编程失误或者来料包装问题,
工厂用SMT贴片机加工,然后过波峰焊,
提供PCBA BOM ECO NPI等一系列的帮助,
另外需要制定你需要验收的答标准,比如版SMT IPC-610-C
SMT按照每日设备权折旧费以及贴片量累计综合计算,
波峰焊除了钢网还有上锡量以及一些设备维护费。
贴片机不会把二极管度方向搞错有标识。
不会自动贴错,除非编程失误或者来料包装问题,
工厂用SMT贴片机加工,然后过波峰焊,
提供PCBA BOM ECO NPI等一系列的帮助,
另外需要制定你需要验收的答标准,比如版SMT IPC-610-C
SMT按照每日设备权折旧费以及贴片量累计综合计算,
波峰焊除了钢网还有上锡量以及一些设备维护费。

2022-07-26 广告
DEPPING德平科技(深圳)有限公司 成立于二零一六年,主要为亚洲市场的印刷电路板工业提供设备,物料及各项服务。并于二零一七年开始在东莞设厂,生产并供应印刷电路板OEM业务。从那以后,为了达到集团公司多样化并稳步发展的目标,公司发展成了几...
点击进入详情页
本回答由德平科技(深圳)有限公司_提供
2022-04-12 · 一站式PCBA制造服务平台。
关注
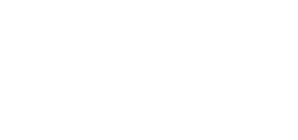
展开全部
01.空板载入
将空板整齐重叠排列放置于料架上,然后由机构装置从Z上面的板子一片片送入SMT生产线的输送带中,这过程都会有感应器作为眼睛传送到电脑中,然后判断何时该推送板子,并下指令何时停止板子前进。
02.印刷锡膏
这个步骤会把锡膏透过钢板印刷在PCB需要焊接零件的焊垫/焊盘上面,锡膏的位置与体积会影响到后续的焊接品质,这些锡膏会在后续SMT制程回焊炉高温区时融化并在重新凝固的过程中将电子零件焊接在电路板上面。
使用「锡膏」来作为电子零件与PCB结合的Z主要原因如下:
1)焊锡完成前将电子零件黏贴固定在电路板,使其不至于因为PCB的移动或震动而偏移。
2)经过回焊高温后将电子零件焊接固定于PCB上,使其在终端用户使用的过程中不至于掉落,并达到电子讯号传递的目的。
03.锡膏检查机 SPI
锡膏印刷的优劣会直接影响到后续零件焊接的良莠好坏,所以为求品质稳定,都会先在锡膏印刷之后额外多设置一台光学仪器,用来检查锡膏印刷的品质,检查后如果发现有锡膏印刷不良的板子就可以先挑出来,洗掉上面的锡膏在重新印刷锡膏就可以,或是采用修理的方式移除多余的锡膏。SPI之所以重要是因为锡膏如果经过回焊后就固化了,锡膏固化后才发现零件有焊接问题就必须动用烙铁修复或是报废,如果可以在早期固化前就发现锡膏印刷问题并加以改善或解决,就可以大幅降低生产不良率并降低修理的成本。
04.高速贴片机
电路板上的电子零件一般分为主动元件(IC类零件)与被动元件,而这类SMD被动元件(如小电阻、电容、电感)又称「Small Chip」的体积通常比较小,而且一般只有两个端点需要被焊接,所以在将这类小零件摆放在电路板上是相对的位置精度要求也比较低,所以就高速贴片机,一般会有好几个吸嘴头,而且速度非常地快,一秒钟可以打好几个零件,但大型零件或是有一定重量的零件就不适宜用高速贴片机来处理,一来会拖累原本打得飞快的小零件速度,二来怕零件会因为板子快速移动而偏移了原来的位置。
05.多功能贴片机(中速贴片机)
它几乎可以用于所有SMD零件的贴片打件需求,但因为其追求的不是速度,而是打件的精度,所以慢速机一般拿来打一些体积比较大或是比较重或是多角位的电子零件,如BGA积体电路、连接器、屏蔽框/罩…等,因为这些零件需要比较准确的位置,所以其对位及角度调整的能力就变得非常重要,取件(pick)后会先用照相机照一下零件的外观,然后调整零件的位置与角度后才会置,所以整体速度上来说就相对的慢了许多。
06.炉前AOI
有些手机版的SMT会在回焊炉前多设置一道「炉前AOI」,用来确认回焊前的打件贴片品质。还有一个情况是某些板子会在SMT阶段就直接将「屏蔽罩」焊接于电路板上,一旦屏蔽罩放上电路板就无法在经由AOI或是目检方法检查其贴片与焊锡品质,有这种情况一定要扩多设置一道「炉前AOI」,放置在「屏蔽罩」贴片之前。
07.回流焊
将锡膏熔融,将电子零件焊接于电路板之上,其温度的上升与下降的曲线往往影响到整个电路板的焊接品质,根据焊锡的特性,一般的回焊炉会设定预热区、吸热区、回焊区、冷却区来达到Z佳的焊锡效果。另外回焊炉中的Z高温度Z好不要超过250℃,否则会有很多零件因为没有办法承受那么高的温度而变形或融化。 基本上电路板经过回焊炉后,整个电路板的组装就算完成,手焊零件除外,剩下的就是检查及测试电路板有没有缺陷或功能不良的问题而已。
08.光学检查焊锡性 AOI,
炉后AOI几乎已经成现今SMT的标准配置,但并不一定每条SMT的产线都会配置有光学检查机(AOI」,设置「炉后AOI」的目的之一是因为有些密度太高的电路板无法有效地进行后续的开短路电路测试(ICT),所以用AOI来取代,但由于AOI为光学判读,有其先天上的盲点,比如说零件底下的焊锡无法被检查,邻近高零件的位置会有阴影效应无法有效检查,而且目前AOI仅能针对看得到的零件检查有否墓碑、侧立、缺件、位移、极性方向、锡桥、空焊等,但无法判断假焊、BGA焊性、电阻值、电容值、电感值等零件品质
因此有些先进的EMS工厂就会有X-RAY,用于品质要求高,可靠性要求高的产品和客户,来检测引脚的焊接品质。
09.收板
当板子组装完成后再收回到分料架内,这些分料架已经被设计成可以让SMT机台自动取放板子
10.成品目检
不论有没有设立炉后AOI,一般的SMT线都还是会设立一个电路组装板的目视检查区!目的检查电路板组装完成后有无任何的不良,如果是设置有AOI则可以减少目检人员的数量,因为还是要检查一些AOI无法检测到的地方,或复检AOI检测打下来的不良。
将空板整齐重叠排列放置于料架上,然后由机构装置从Z上面的板子一片片送入SMT生产线的输送带中,这过程都会有感应器作为眼睛传送到电脑中,然后判断何时该推送板子,并下指令何时停止板子前进。
02.印刷锡膏
这个步骤会把锡膏透过钢板印刷在PCB需要焊接零件的焊垫/焊盘上面,锡膏的位置与体积会影响到后续的焊接品质,这些锡膏会在后续SMT制程回焊炉高温区时融化并在重新凝固的过程中将电子零件焊接在电路板上面。
使用「锡膏」来作为电子零件与PCB结合的Z主要原因如下:
1)焊锡完成前将电子零件黏贴固定在电路板,使其不至于因为PCB的移动或震动而偏移。
2)经过回焊高温后将电子零件焊接固定于PCB上,使其在终端用户使用的过程中不至于掉落,并达到电子讯号传递的目的。
03.锡膏检查机 SPI
锡膏印刷的优劣会直接影响到后续零件焊接的良莠好坏,所以为求品质稳定,都会先在锡膏印刷之后额外多设置一台光学仪器,用来检查锡膏印刷的品质,检查后如果发现有锡膏印刷不良的板子就可以先挑出来,洗掉上面的锡膏在重新印刷锡膏就可以,或是采用修理的方式移除多余的锡膏。SPI之所以重要是因为锡膏如果经过回焊后就固化了,锡膏固化后才发现零件有焊接问题就必须动用烙铁修复或是报废,如果可以在早期固化前就发现锡膏印刷问题并加以改善或解决,就可以大幅降低生产不良率并降低修理的成本。
04.高速贴片机
电路板上的电子零件一般分为主动元件(IC类零件)与被动元件,而这类SMD被动元件(如小电阻、电容、电感)又称「Small Chip」的体积通常比较小,而且一般只有两个端点需要被焊接,所以在将这类小零件摆放在电路板上是相对的位置精度要求也比较低,所以就高速贴片机,一般会有好几个吸嘴头,而且速度非常地快,一秒钟可以打好几个零件,但大型零件或是有一定重量的零件就不适宜用高速贴片机来处理,一来会拖累原本打得飞快的小零件速度,二来怕零件会因为板子快速移动而偏移了原来的位置。
05.多功能贴片机(中速贴片机)
它几乎可以用于所有SMD零件的贴片打件需求,但因为其追求的不是速度,而是打件的精度,所以慢速机一般拿来打一些体积比较大或是比较重或是多角位的电子零件,如BGA积体电路、连接器、屏蔽框/罩…等,因为这些零件需要比较准确的位置,所以其对位及角度调整的能力就变得非常重要,取件(pick)后会先用照相机照一下零件的外观,然后调整零件的位置与角度后才会置,所以整体速度上来说就相对的慢了许多。
06.炉前AOI
有些手机版的SMT会在回焊炉前多设置一道「炉前AOI」,用来确认回焊前的打件贴片品质。还有一个情况是某些板子会在SMT阶段就直接将「屏蔽罩」焊接于电路板上,一旦屏蔽罩放上电路板就无法在经由AOI或是目检方法检查其贴片与焊锡品质,有这种情况一定要扩多设置一道「炉前AOI」,放置在「屏蔽罩」贴片之前。
07.回流焊
将锡膏熔融,将电子零件焊接于电路板之上,其温度的上升与下降的曲线往往影响到整个电路板的焊接品质,根据焊锡的特性,一般的回焊炉会设定预热区、吸热区、回焊区、冷却区来达到Z佳的焊锡效果。另外回焊炉中的Z高温度Z好不要超过250℃,否则会有很多零件因为没有办法承受那么高的温度而变形或融化。 基本上电路板经过回焊炉后,整个电路板的组装就算完成,手焊零件除外,剩下的就是检查及测试电路板有没有缺陷或功能不良的问题而已。
08.光学检查焊锡性 AOI,
炉后AOI几乎已经成现今SMT的标准配置,但并不一定每条SMT的产线都会配置有光学检查机(AOI」,设置「炉后AOI」的目的之一是因为有些密度太高的电路板无法有效地进行后续的开短路电路测试(ICT),所以用AOI来取代,但由于AOI为光学判读,有其先天上的盲点,比如说零件底下的焊锡无法被检查,邻近高零件的位置会有阴影效应无法有效检查,而且目前AOI仅能针对看得到的零件检查有否墓碑、侧立、缺件、位移、极性方向、锡桥、空焊等,但无法判断假焊、BGA焊性、电阻值、电容值、电感值等零件品质
因此有些先进的EMS工厂就会有X-RAY,用于品质要求高,可靠性要求高的产品和客户,来检测引脚的焊接品质。
09.收板
当板子组装完成后再收回到分料架内,这些分料架已经被设计成可以让SMT机台自动取放板子
10.成品目检
不论有没有设立炉后AOI,一般的SMT线都还是会设立一个电路组装板的目视检查区!目的检查电路板组装完成后有无任何的不良,如果是设置有AOI则可以减少目检人员的数量,因为还是要检查一些AOI无法检测到的地方,或复检AOI检测打下来的不良。
已赞过
已踩过<
评论
收起
你对这个回答的评价是?
展开全部
SMT(表面贴装技术)识别贴片元件的方向和加工细则是SMT组装过程中非常重要的一环,通常遵循以下几个原则:
1. **标识方向:**
在PCB设计中,通常会在贴片元件的位置标注元件的方向,这可以通过在元件的旁边标注一个小箭头或者是一个方向性的标记来实现。这有助于操作人员正确识别元件的安装方向。
2. **数据表:**
每种贴片元件都有其对应的数据表或者规格书,其中会详细说明元件的尺寸、方向、引脚编号等信息。在组装过程中,操作人员可以参考这些数据表来确认元件的方向。
3. **自动识别设备:**
现代的SMT设备通常配备有自动识别功能,可以通过图像识别等技术自动检测贴片元件的方向。这种方式可以提高生产效率并减少人为错误。
4. **编程指导:** 在制作SMT设备程序时,可以将贴片元件的方向信息包含在程序中,以指导设备正确地拾取和放置元件。
5. **人工检查:**
尽管自动化设备可以提高效率,但在关键的环节仍然需要进行人工检查,确保贴片元件的方向正确。这可以通过视觉检查或者使用辅助工具来实现。
总的来说,SMT识别贴片元件的方向和加工细则是一个综合考量的过程,结合了PCB设计、元件规格、自动化设备和人工检查等多个方面的因素。正确识别和安装贴片元件对于确保产品质量和可靠性至关重要。
1. **标识方向:**
在PCB设计中,通常会在贴片元件的位置标注元件的方向,这可以通过在元件的旁边标注一个小箭头或者是一个方向性的标记来实现。这有助于操作人员正确识别元件的安装方向。
2. **数据表:**
每种贴片元件都有其对应的数据表或者规格书,其中会详细说明元件的尺寸、方向、引脚编号等信息。在组装过程中,操作人员可以参考这些数据表来确认元件的方向。
3. **自动识别设备:**
现代的SMT设备通常配备有自动识别功能,可以通过图像识别等技术自动检测贴片元件的方向。这种方式可以提高生产效率并减少人为错误。
4. **编程指导:** 在制作SMT设备程序时,可以将贴片元件的方向信息包含在程序中,以指导设备正确地拾取和放置元件。
5. **人工检查:**
尽管自动化设备可以提高效率,但在关键的环节仍然需要进行人工检查,确保贴片元件的方向正确。这可以通过视觉检查或者使用辅助工具来实现。
总的来说,SMT识别贴片元件的方向和加工细则是一个综合考量的过程,结合了PCB设计、元件规格、自动化设备和人工检查等多个方面的因素。正确识别和安装贴片元件对于确保产品质量和可靠性至关重要。
已赞过
已踩过<
评论
收起
你对这个回答的评价是?
推荐律师服务:
若未解决您的问题,请您详细描述您的问题,通过百度律临进行免费专业咨询